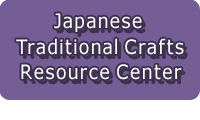
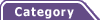
Total:131items
- Pottery & Porcelain (18)
- Lacquerware (4)
- Glasswork (2)
- Wood & Bamboo Work (19)
- Leather Work (1)
- Papermaking (13)
- Textile (20)
- Touzan-Ori: Touzan Weaving
- Sakai Gogatsu Koinobori: Sakai May Carp Streamer
- Nanbu Sakiori
- Nihon Shishu: Japanese Embroidery
- Tsuzurenishiki-Ori: Tsuzurenishiki Weaving
- Ojiya-Tsumugi: Ojiya Pongee
- Ise-Momen: Ise Cotton
- Ojiya-chijimi: Ojiya Crepe
- Yanai-jima: Yanai Stripes
- Kogin-zashi: Kogin embroidery
- Tamba Momen: Tamba Cotton
- Awa Shijira-ori: Awa Shijira Weaving
- Saga Nishiki: Saga Brocade
- Shinshu-Tsumugi: Shinshu-Pongee
- Kyo-nui: Kyoto Embroidery
- Noto Jofu: Noto-jofu hemp fabric
- Matsusaka Momen: Matsusaka Cotton
- Murayama Oshima Tsumugi
- Nibutani-attus
- Oku-Aizu Showa Karamushi Ori: Oku-Aizu Showa Ramie Textiles
- Dyeing products (5)
- Masonry (1)
- Metal Work (11)
- Stationery (4)
- Livingware (3)
- Accessory (4)
- Toys & Entertainment (14)
- Interior (2)
- Other crafts (10)

![]() |
Main Production Site:Hokkaido |
_MG_2001.jpg)
Nibutani-attus is an Ainu textile traditionally woven in the Sarugawa River basin, and now its traditional weaving techniques are taken over mainly in Nibutani, Biratori-cho in Hokkaido. The textile is woven with yarn made of the inner bark of Manchurian elms and Japanese elms of Sarugawa area, and the woven Attus is used to make Kimono, Hanten (short coat), half aprons, Obi (belts) and other small products.
Only the textiles with yarn made of the inner bark of Manchurian Elms, called ‘Atni’ in Ainu language, and woven with the weaving loom called ‘Attuskarape’ can be called ‘Attus’, and usually Attus is woven by Ainu women.
The features of Nibutani-attus are its excellence in both waterproofness and breathability, its durability that is rare for natural fabrics, and its unique texture. Also, the textile is distinguished by its making process containing yarn twisting. All the process of making Nibutani-attus is done using the traditional tools which are almost the same as the ones used 100 years ago.
[Traditional craft designated by the Minister of Economy, Trade and Industry]
Information provided by: Nibutani Crafts Cooperative Association
Translation by: Mie Nakajima, reviewed by: Tae Yamaguchi
Materials | ‘Atni’ (Manchurian elms) |
---|---|
Crafting Processes | Nibutani-attus is produced through many processes: peeling the inner bark into yarn, looping and twisting the yarn, threading the yarn through a shuttle and passing it on a weaver, weaving, etc. All of them are proceeded by hand.
1. Peeling the bark The trunk of Atni is jagged and debarked from the lower part to the upper part of it. Just after the end of the rainy season is the best for peeling because the tree is moistened well. To avoid the risk of a tree falling caused by dieback, the standing timber is often laid down prior to the process. 2. Peeling the rough bark The outer rough bark is peeled carefully to get the inner bark, which is to be the yarn for weaving. 3. Softening the inner bark In order to soften the inner bark, it is boiled with a lye for a few hours in an iron pot. Some craftsmen soak it in a swamp or hot springs for a week for softening. 4. Washing the bark The inner bark is washed in a river such as a mountain stream so that the guck on the bark will be removed. 5. Peeling the layers of the inner bark The layered inner bark is massaged to be separated into several thin layers. 6. Looping and yarn twisting The thin sheets of the inner bark are now torn with fingers to make weaving yarns, which are the same in thinness. The yarns are looped and bound using the way of ‘sheet bend’: the method can help to make the tie knots smaller. 7. Stretching and setting yarn over the weaving loom (Warping) The one side of the yarn pulled out of a yarn ball is stretched over and wound around a wooden stake, which is several meters away from the weaving loom and set on the ground; then the other side is laced through the weaving loom. At this stage, colours and patterns in vertical lines are determined. 8. Preparing the warp yarn The lower warp yarns are lifted one by one using cotton thread; the cotton thread catching the lower warp yarns is wound around a heddle, called ‘Pekaunnni’, in a figure-8 style. 9. Weaving The heddle, ‘Pekaunnni’, is lifted to create a space between the upper and the lower warp yarns, and the shuttle with the weft is passed through the space. Every time the weft is passed through, the position of both sets of the upper and the lower warp yarns should be switched. The interlaced warp and the weft, then, should be beaten with a big spatula so that the woven pattern will get tightened. The finished textile is called Attus, and sometimes the products made of the textile, such as Kimono, Obi belts and so on, are called Attus, too. The yarn for attus is usually unbleached or dyed with plants. |
History | Nibutani-attus has been made by Ainu people who live near the Sarugawa River, called ‘sar-un-kur’, for more than 100 years. In the Edo period, Attus was already sold to other areas as the Sarugawa product; it shows that the textile was treated as something unparalleled in those days.
It is thought that materials for Nibutani-attus were gathered from the villager’s shared fields for hunting and gathering, called ‘iworo’. It is also said that building materials for houses and food were gathered from iworo. Nibutani-attus has been used as daily necessities, thus, its traditional techniques and methods have been taken over till today. In the period of high economic growth in Japan (1960s-1970s), tourism boomed and Attus played a big role in both regional economy and conservation of cultural heritage as a souvenir. As for other areas, the number of those who can hand down the tradition temporarily decreased, but people in Biratori (Nibutani) actively continued making Attus and consequently encouraged other areas to keep on making Attus; as a result, Biratori’s traditional techniques became popular even in other areas. Using the weaving loom in the same way as 100 years ago, people in Nibutani preserve their traditional techniques. Today, Nibutani crafts association which consists of craftsmen in the area takes the initiative not only to make and sell Attus craft, but to pass down the traditional techniques through generations. |
Related URL | http://nibutani.jp/ |
◆Exhibition / Showcase
Nibutani kougeikan (Nibutani Crafts Center)
Biratori Town Ainu Cultural Information Centre,
61-6 Nibutani, Biratori-cho, Saru-gun, Hokkaido 055-0101
TEL: +81-(0)1457-2-3299
Entry: Free
Opening hours: 9:00 a.m.-5:00 p.m.
Closed: New Year’s Eve to January 5