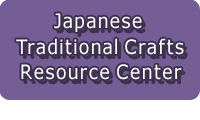
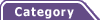
Total:131items
- Pottery & Porcelain (18)
- Lacquerware (4)
- Glasswork (2)
- Wood & Bamboo Work (19)
- Leather Work (1)
- Papermaking (13)
- Textile (20)
- Dyeing products (5)
- Masonry (1)
- Metal Work (11)
- Satsuma Suzuki: Satsuma Tinware
- Tosa Uchihamono: Tosa Blade
- Kaga Zougan: Kaga Inlay
- Akita Ginsen Zaiku: Akita Filigree
- Token: Japanese Sword
- Banshu-gama : Banshu Sickle
- Echigo-Sanjo Uchi Hamono: Echigo-Sanjo Blade
- Osaka Naniwa Suzuki: Pewter/Tin Ware
- Nakaniida-Uchihamono: Nakaniida Traditional Blade
- Higo-Tsuba
- Nokaji Hamono: Nokaji Blades
- Stationery (4)
- Livingware (3)
- Accessory (4)
- Toys & Entertainment (14)
- Interior (2)
- Other crafts (10)

![]() |
Main Production Site:Wakayama |
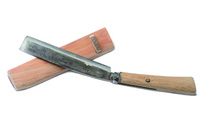
Nokaji blades (Nokaji Hamono) are traditional crafts mainly made for forestry work. such as axes, hatchets and scythes.
A Nokaji axe, for example, has long, narrow grooves on both sides of the blade: three on one side and four on the other. These grooves of each side have symbolic meaning. The three grooves, called “miki”, represent sacred sake that is offered to the gods in Shinto rituals. The four, called “yoki”, represent harvests from the sea and mountains. Such grooved axes, therefore, could take the place of actual offerings of both sake and seasonal foods to the god of the mountain. So before starting to fell trees, traditionally woodcutters would lean axes against the trees to express their gratitude to the god and pray for the safety of their work.
According to another tradition, the seven grooves on a Nokaji axe head represent the seven stars of the Big Dipper, implying their relationship with the ancient worship of the North Star.
[Local traditional Craft designated by Governor of Wakayama Prefecture]
Source: Corporate Promotions Division, Corporate Policy Bureau, Commerce, Industry, Tourism and Labour Department, Wakayama Prefectural Government
Translation by Tomoko Yamamoto, reviewed by Tae Yamaguchi
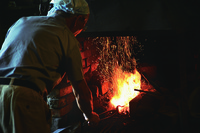
Materials | Iron, steel, etc. |
---|---|
Crafting Processes | 【1】Cutting
The raw materials are cut with iron saws and chisels to the desired size. 【2】Forge welding of iron and steel Iron and steel are forge-welded*1 by striking with a power hammer and a hand-held hammer. *1 Combining two kinds of metals by applying heat and enough pressure. 【3】Forging and moulding The materials are heated in a coke oven*2, and then moulded with a power hammer and a hand-held hammer. *2 An oven for that heats steel and other materials by steaming coal at high temperatures inside. 【4】Finishing The heated material is left to cool for half a day, and then ground with a file and a grinder. 【5】Quenching (Rapid cooling) The material is heated with coal until it reaches a temperature of 730-850℃, then it is rapidly cooled in water to harden the metal. Next, it is heated again until it reaches a temperature of 150℃ to increase its viscosity. 【6】Creating the cutting edge The cutting edge is created by grinding the material on a grindstone, in upright position, for approximately 30 minutes. ![]() |
History | Shingu City, located at the mouth of the mighty Kumano River, served as a trading hub for lumber resources transported by boats along the river, which brought the remarkable development of the Kumano lumber industry. Along with the concentration of forestry workers (known as yama-shi), blacksmiths also gathered here to supply them with forestry tools. By 1916, Shingu City had a blacksmith union consisting of about thirty members.
As chain saws became popular for forestry work around the mid-1950s, the demand for Nokaji blades gradually decreased. However, the history of many blacksmiths living there is reflected in the town names, such as ‘Motokaji-machi’ (“Former Blacksmith Town”), or ‘Shinkaji-machi’ (“New Blacksmith Town”). |
Related URL | https://www.wakayama-sangyo.com/monozukuri/en/production/traditional-crafts/nokaji_knives/ |
◆Exhibition / Showcase
Okawa Kaji(Okawa Blacksmith)
1-10-11 Aisuji, Shingu City, Wakayama Prefecture 647-0001
Tel/Fax +81-(0)735-22-5066
◆Event Information
Assistance needed? For inquiries in English:
JTCO Contact Form
Your inquiries will be forwarded by JTCO in Japanese to the organization you wish to contact.
*Please write the name of craft you wish to ask about.