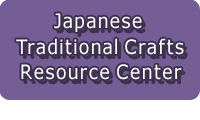
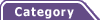
Total:131items
- Pottery & Porcelain (18)
- Lacquerware (4)
- Glasswork (2)
- Wood & Bamboo Work (19)
- Leather Work (1)
- Papermaking (13)
- Textile (20)
- Dyeing products (5)
- Masonry (1)
- Metal Work (11)
- Stationery (4)
- Livingware (3)
- Accessory (4)
- Toys & Entertainment (14)
- Interior (2)
- Other crafts (10)

![]() |
Main Production Site:Yamanashi |
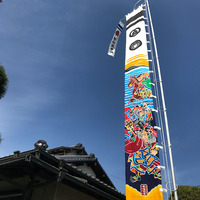
Features:
Hand-dyed banners with vivid colors.
Honzome Koshu musha-nobori (dyed warrior banners)
Musha-noboris were originated from hatasashimono (small war banners) worn by soldiers. In Yamanashi, parents began to hang them up on Children's Day since the late Edo period. On banners, stories of Shingen Takeda, the feudal lord of Kai Province (today Yamanashi Prefecture), was illustrated in the hope that children would grow up as strong as him.
As you recognize paintings of the Battles of Kawanakajima and Mt. Fuji Hunt, what makes those artworks unique is the sketching handed down through the generations as well as vivid colors.
Honzome Koshu koi-nobori (Carp banner)
As well as musha noboris, koi-noboris are hand dyed. Every process is done by hand carefully- from glue making (with fine glutinous rice powder and rice bran) to fabric washing, sketching, glue pasting, dyeing, washing and drying.
With the technique that was originated in the end of Edo period, craftsman (seventh) dyes fabrics with bright colors that make noboris dynamic and unique.
Traditional folk craft officially designated by: Yamanashi prefecture
Provided by: Inoue Fabric Dyer's Shop
Translation by Kouhei Nishimura, reviewed by Eri Hara
Materials | Fabrics, Nara sumi (ink made in Nara), resist (made with glutinous rice flour
and bran), animal glue |
---|---|
Crafting Processes | 1. Resist paste making and dyeing
Resist paste making is the most important part of "nori-zome" (resist-dyeing) technique. Craftsman kneads and steams the mix of fine glutinous rice flour and rice bran thoroughly. By repeating these processes, lines will be left very white, giving the dyed fabrics the characteristic three-dimensional look. 2. Refinement, sketching and nori-oki (applying the paste with a brush) To remove impurities contained in fibers, craftsman refines fabrics. After tracing the design over fabrics and draw lines with paste, craftsman dries them for a couple of days. 3. Applying Gojiru (soy milk), dyeing and color fixing After applying Gojiru to fabrics, craftsman dyes them completely with the Nara ink (with the addition of animal glue liquid) using soft Edo brushes. This applying process is repeated to finish up dyeing. 4. Washing and drying Craftsman washes dyed fabrics in the factory tank to remove the paste and any extra dyes. In the old days, craftsmen washed them in the river. When the strong resist is washed off, lines will be left white giving the traditional patterns strong look. He checks any resist or impurities left on fabrics while washing. All washed fabrics are thoroughly sun dried. 5. Hemming and Finishing To avoid fray, craftsman hems around perimeters of entire noboris. Then he hangs their upper and right sides on poles with chis (hanging rods) or horizontal hangers. For the finishing touch, he attaches tails decorated with shiny ornaments on their ends. ![]() |
History | In the late Edo period, Shinabei Inoue started to design and make indigo dyeing fabrics at his own fabric shop. After the Meiji period, Bunzamemon (second generation) and Toyomatsu (third) started to design and make indigo-dyed musha noboris and carp noboris.
These product launches led to great success that allowed them to afford to hire dozens of craftsmen at third and Magotaro (fourth) generations. Since then, people started to call warrior-painted nobodies "Koshu musha noboris". Having inherited traditional techniques, Yutaka (fifth) became one of leading dyers and Toyohiko (sixth) successfully adopted contemporary fashion in his collections that were designated as Yamanashi traditional crafts in 1994. Nobuhiro, (seventh) is now working on contemporary dyeing fabric development while he values inherited techniques and production with pride, skill and dedication (monozukuri /craftsmanship). In Yamanashi, he is the only craftsman who designs and makes hand made Honzome Koshu Musha noboris and koi noboris. ![]() |
Related URL | https://kousyu-koinobori.jp/ |
◆Exhibition / Showcase
Exhibition Place
Inoue Fabric Dyer's Shop
460, Furuichiba, Minami-Alps-Shi, Yamanashi, 400-0404
Tel: +81-(0)55-282-1030
Opening hours: 9:00-17:00
Holidays: Sundays (except Children's Day)
(Available in Japanese only)
◆Event Information
Assistance needed? For inquiries in English:
JTCO Contact Form
Your inquiries will be forwarded by JTCO in Japanese to the organization you wish to contact.
*Please write the name of craft you wish to ask about.