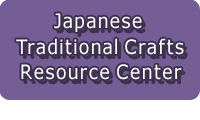
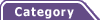
Total:131items
- Pottery & Porcelain (18)
- Lacquerware (4)
- Glasswork (2)
- Wood & Bamboo Work (19)
- Leather Work (1)
- Papermaking (13)
- Textile (20)
- Touzan-Ori: Touzan Weaving
- Sakai Gogatsu Koinobori: Sakai May Carp Streamer
- Nanbu Sakiori
- Nihon Shishu: Japanese Embroidery
- Tsuzurenishiki-Ori: Tsuzurenishiki Weaving
- Ojiya-Tsumugi: Ojiya Pongee
- Ise-Momen: Ise Cotton
- Ojiya-chijimi: Ojiya Crepe
- Yanai-jima: Yanai Stripes
- Kogin-zashi: Kogin embroidery
- Tamba Momen: Tamba Cotton
- Awa Shijira-ori: Awa Shijira Weaving
- Saga Nishiki: Saga Brocade
- Shinshu-Tsumugi: Shinshu-Pongee
- Kyo-nui: Kyoto Embroidery
- Noto Jofu: Noto-jofu hemp fabric
- Matsusaka Momen: Matsusaka Cotton
- Murayama Oshima Tsumugi
- Nibutani-attus
- Oku-Aizu Showa Karamushi Ori: Oku-Aizu Showa Ramie Textiles
- Dyeing products (5)
- Masonry (1)
- Metal Work (11)
- Stationery (4)
- Livingware (3)
- Accessory (4)
- Toys & Entertainment (14)
- Interior (2)
- Other crafts (10)

![]() |
Main Production Site:Tokyo |
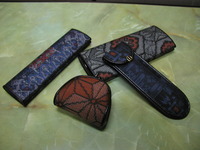
The most distinctive feature of Murayama Oshima Tsumugi,a type of silk fabric, is its pre-dyed kasuri threads--silk threads used to make patterns and dyed with a unique dyeing technique, Itajime, a method of making dyed patterns by pressing cloth between carved boards.
*kasuri: Fabrics woven with resist-dyed threads, commonly known as “ikat” in Malay, characterized by blurred or brushed patterns.
Itajime uses thin wooden boards called Kasuri Ita in the following way: a design, Ita Zuan, is drawn on special graph paper; wooden boards made of Mizume-zakura (Japanese Cherry Birch) more than a century old are prepared; the prepared design is engraved on the boards, using exquisitely skillful and intricate techniques. Various delicate kasuri patterns are created through the Kasuri Ita.
It takes an enormous amount of time and effort to weave Murayama Oshima Tsumugi, faithfully following this traditional method. After the final fabric inspection, finished fabrics are finally put on the market. The whole process is done entirely by hand, so Murayama Oshima Tsumugi can be an incomparably elaborate fabric.
Murayama Oshima Tsumugi--woven for the delight of everyone who wears it--continues to fascinate people with its chic elegance.
[Traditional Craft designated by the Ministry of Economy, Trade and Industry]
Courtesy of Murayama Textiles Cooperative Association
Translation by : Tae Yamaguchi
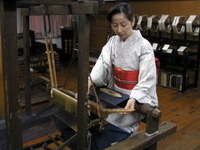
Materials | Japanese Cherry Birch for Kasuri Ita, and raw silk |
---|---|
Crafting Processes | 1.Preparing Kasuri Ita (Carved Boards)
Itajime dyeing is characteristic of Murayama Oshima Tsumugi. Its chic and elaborate patterns are produced with considerable skills--from carving boards to winding and arranging threads on each of the carved boards. All these techniques require experience and expertise. In general, approximately 150 plates of Kasuri Ita are needed to wind warp and weft threads. Kasuri Ita is made of large Mizume-zakura (Japanese Cherry Birch) more than 70 years old. 2.Refining Raw Silk The raw silk is boiled to remove impurities; in this stage, sericin (a glue-like protein)--a key component of raw silk--is dissolved and fibroin (a fibrous protein)--the core of silk fiber--is extracted. Silk achieves its soft, lustrous texture through this process. 3.Ji-Zome (Dyeing Ground Threads) The silk threads for the background (ground threads) are dyed with natural dyes from plants, such as hematin, using an iron catalyst. Fabrics for women’s kimono, for example, use both the warp and the weft as ground threads. 4.Warping The length and number of the warp and the weft are fixed, depending on the size of the desired patterns. Four sets of threads are made: the warp and the weft for both ground threads and kasuri threads (pattern threads). Each set of threads is different in thickness or the degree of twist. 5.Ita-Maki (Winding Threads) and Ita-Zumi (Stacking Kasuri Ita) The prepared threads are wound around each Kasuri Ita, without any gaps or crossing of each other--that is, in a parallel arrangement. The arrangement of threads determines the quality of the fabric, so a great deal of skill is required in this process. 6.Itajime Dyeing The warp and weft kasuri threads, each wound around Kasuri Ita and stacked separately, are laid on a dye bath called Fune (meaning “vessel”). Then, all of the stacks are tightened with bolts, and dye is poured into the dye bath. Consequently, the threads between the grooves of Kasuri Ita are dyed, while the threads tightened between the boards remain undyed. Depending on the tightness, the size of the kasuri patterns changes, or the dye could penetrate to the threads which are not to be dyed. This process is so delicate that it is regarded as “crucial” for Murayama Oshima Tsumugi. 7.Surikomi-Nassen (Rubbing Print) Itajime results in a solid color. When more colors are applied, another dying technique is used: Surikomi-nassen (Rubbing Print). The process is done in the following way: the Itajime-dyed kasuri threads are divided into small bundles according to the patterns of the threads; each bundle is tied off in places to avoid deforming the patterns; color is applied to each bundle by rubbing them with a special bamboo spatula around which cotton thread is wound, according to the original design; the colored bundles are steamed in a box steamer so that the applied color will be bonded. 8.Hata-Maki (Beaming) The warp, including kasuri and ground threads, is wound onto a warp beam with both of them combined, making sure to form the designed kasuri patterns precisely. This process is vital because it will inevitably affect the next step, the weaving. 9.Weaving The warp on the warp beam is threaded through heddles and a reed, then put on a loom. The weft kasuri and ground threads--wound on each shuttle bobbin--are interlaced together with the warp kasuri threads. Since the weaver must be careful with both kasuri threads (warp and weft) individually to compose the designed kasuri patterns accurately, considerable effort and time is required. 10.Fabric Inspection Murayama Oshima Tsumugi never goes to market without going through a final fabric inspection. It is only when the fabrics pass the inspection--including checking the measurement, durability, kasuri patterns and so on--that both “Traditional Craft” and “Traditional Craft Certificate” marks are attached. |
History | Musashimurayama City, Tokyo, is located in the center of the area surrounding Sayama Hills. It is an area where people have lived since ancient times. The spindle whorl and other artifacts of the Kofun period (ca.3rd-7th century A.D.) were excavated from the remains of the city, and it is supposed that weaving was done in this area more than 1,500 years ago.
Because of poor water supply, this area had infertile, stony fields and few rice fields. As a result, materials such as cotton or indigo came to be produced during the agricultural off-season, and then weaving was established. Until the middle of the Edo period (the mid-18th century), only a few cotton, hemp and silk fabrics were woven for private use during the off-season. Although there are several theories about its origin, Cotton Kasuri probably began to be made around the Bunka-Bunsei period (the early 19th century). It is said that Murayama Oshima Tsumugi was created in the middle of the Edo period. First, two strands of weave, Murayama-kongasuri (cotton fabric dyed with Sho-aizome--a type of indigo dyeing) and Sunagawa-futo’ori (silk fabric made from Tama-mayu: double cocoons), were mixed together. Then, through the transition of weaving techniques such as Shima-meisen, Midare-gasuri, and Tate-muji, the fabric was developed into the silk fabric of Tate-yoko-gasuri (double kasuri). The last, Murayama Oshima Tsumugi, as we know it today, began mainly to be produced in the 1920s. Due to the ceaseless efforts of pioneers, its high quality and durability became more highly valued year after year. From the middle of the Taisho period (1912-26), Murayama Oshima Tsumugi came to be woven on a unique handloom throughout Murayama Village (present-day Musashimurayama City) and Sunagawa Village (present-day Sunagawa Town, Tachikawa City, Tokyo). This Itajime-kasuri, 100% pure silk fabric, is woven with warp and weft kasuri threads skillfully dyed using different dyeing techniques. It is characterized by its exquisite weaving, modest, traditional appearance, and front-back symmetry. In recognition of its value, Murayama Oshima Tsumugi was designated a “Traditional Craft” by Tokyo in March 1967. In February 1975, it was also designated a Traditional Craft by the Ministry of Economy, Trade and Industry. |
Related URL | http://www.muraori.sakura.ne.jp/ |
◆Exhibition / Showcase
For more Information:
Murayama Textiles Cooperative Association
Address:
2-2-1 Hommachi,
Musashimurayama-shi, Tokyo, 208-0004
JAPAN
Tel : +81-42-560-0031
Fax: +81-42-560-6252
(Japanese Only)
◆Event Information
Assistance needed? For inquiries in English:
JTCO Contact Form
Your inquiries will be forwarded by JTCO in Japanese to the organization you wish to contact.
*Please write the name of craft you wish to ask about.