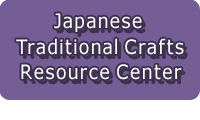
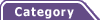
Total:131items
- Pottery & Porcelain (18)
- Lacquerware (4)
- Glasswork (2)
- Wood & Bamboo Work (19)
- Leather Work (1)
- Papermaking (13)
- Textile (20)
- Dyeing products (5)
- Masonry (1)
- Metal Work (11)
- Satsuma Suzuki: Satsuma Tinware
- Tosa Uchihamono: Tosa Blade
- Kaga Zougan: Kaga Inlay
- Akita Ginsen Zaiku: Akita Filigree
- Token: Japanese Sword
- Banshu-gama : Banshu Sickle
- Echigo-Sanjo Uchi Hamono: Echigo-Sanjo Blade
- Osaka Naniwa Suzuki: Pewter/Tin Ware
- Nakaniida-Uchihamono: Nakaniida Traditional Blade
- Higo-Tsuba
- Nokaji Hamono: Nokaji Blades
- Stationery (4)
- Livingware (3)
- Accessory (4)
- Toys & Entertainment (14)
- Interior (2)
- Other crafts (10)

![]() |
Main Production Site:Osaka |
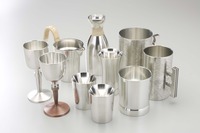
Tin is a very soft metal, making it hard to craft by machining. Therefore most of the crafting steps of suzuki (Japanese pewter /tin ware) must be done manually. After casting, the individual pieces are turned on lathes to shape and polish.
Since ancient times, suzuki were created, including religious ceremonial decanters and ‘sakaki’ (sacred evergreen) stands, as well as tea canisters and saucers. Initially, suzuki was enjoyed only by limited groups of people, such as those in the imperial court, but during the Edo period (17-19c), they began to be used in general public as well.
.
Suziki sake vessels are believed to produce an ionic effect that smoothens and enriches the taste of sake. Also, being crafted on lathes, the lids and bottoms of suzuki pieces are extremely close fitting, and are believed to provide outstanding protection against moisture when used to store tea leaves. Suzuki’s unique texture is well showcased in items like meimei-zara (small-sized individual serving plates), shuniku-ire (vermilion inkpad case for Japanese formal hanko-stamps), and also flower vases. All of these items are popular for both personal use and as gifts.
In March 1983, Osaka Naniwa tin ware was designated as “traditional crafts”, by the Minister of International Trade and Industry (currently the Minister of Economy, Trade and Industry).
[Nationally Designated Traditional Crafts (by the Minister of Economy, Trade and Industry)]
Source: Suzuki Jigyo Kyodo Kumiai (Japanese Pewter / Tin Ware Industry Association)
Translated by:Emi Yagasaki,reviewed by Misa Imanaka
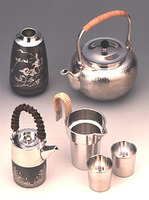
Materials | Tin (Suzu) and tin alloys. Usually hon-suzu (97 % tin alloy). |
---|---|
Crafting Processes | [1] Casting
The melting point of tin is rather low, at 230 degrees (celsius). Base ingots are melted in a pot, until they become molten, and then poured via ladle into molds. The molds are tilted to help the molten tin flow in easily. When it’s ready, the ’nakago’ (inner mold) that serves to create the internal hollow space is removed. Using a brush dipped in water, the remaining piece is cooled down until it is ready to be removed from the mold. The excess metal around the sprue of the mold gets cut off. Molds vary widely in their purposes and sizes. They are made from different materials such as cement, stone, soil, or metal. [2] Cutting Using a lathe, round casted pieces are shaved/scraped to desired shapes. This step is considered the central part of crafting suzuki, and separates it from common tin ware. The surface of the piece is very rough right after casting, but after it is shaved with lathe chisels, they start to reveal suzu’s characteristic bright shine. Large or slender pieces such as vases, and complicated pieces that cannot be cast in a single mold are shaved and shaped in sections (upper and bottom). After going through meticulous fitting of both the inside and outside of each section, they are finally combined into one piece via soldering. [3] Intermediate Process Additional parts that cannot be created on lathes, such as the handle or the spout are made separately and attached to the main piece via soldering. Cutting, bending, and hammer-finishing to create the traditional ‘tsuchime’ pattern are also done during this step. [4] Design Application After the lathe work is complete, designs are drawn in urushi lacquer or enamel. This produces a masking effect for the next process, which is acid etching. The piece is dipped in a nitric acid solution, and while the area under the ink remains protected, the rest of the surface is eaten away to develop a matte /satin finish. This finish is said to be reminiscent of the skin of a Japanese pear. This process is very delicate and susceptible to various factors, including the climate. After reaching the desired amount of etching, the acid is rinsed off with water. The designs are further refined by applying lacquer in colors such as black or vermillion and wiping it off, over and over again. The careful repetition of the process makes the patterns stand out and glow with to elegant effect. [5] Finishing After the lacquer is dry, the pieces are polished on a lathe. Peripheral parts such as handles are attached, and the piece receives the finishing touch. |
History | The history of pewter/ tin ware is very long. Tin water jars have been found in ruins of the Egyptian Kingdom from around 1500 B.C.
Because of the glossy surface and low melting point, tin has been used to create various utensils all over the world since ancient times. Around 7-9th century, pewter/tin ware was brought into Japan by Kenzuishi (Japanese envoy to the Sui Dynasty of China) and Kentoushi (Japanese envoy to the Tang Dynasty of China). Some of those pieces are still preserved in the Nara Shosoin (the renowned treasure house that belongs to the Todaiji Temple in Nara, western Japan). Originally, tin was used to craft items dedicated to divinities, such as sacred sake vessels used in the imperial court. In the 17th century, high-class restaurants and mercantile homes started using suzuki as drinking vessels, plates, and tea utensils, followed by the general population. The suzuki industry gradually grew in Osaka, a town which was a distribution hub near the former capital, Kyoto. |
◆Exhibition / Showcase
For more information…
Suzuki Jigyo Kyodo Kumiai (Japanese Pewter /Tin Ware Industry Association), c/o Osaka Suzuki Co.
6-6-15 Tanabe, Higashi Sumiyoshi Ward, Osaka City
TEL.+81-(6)-6628-6731 (Japanese only)
◆Event Information
Assistance needed? For inquiries in English:
JTCO Contact Form
Your inquiries will be forwarded by JTCO in Japanese to the organization you wish to contact.
*Please write the name of craft you wish to ask about.