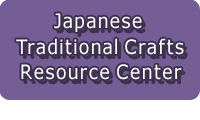
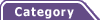
Total:131items
- Pottery & Porcelain (18)
- Lacquerware (4)
- Glasswork (2)
- Wood & Bamboo Work (19)
- Leather Work (1)
- Papermaking (13)
- Textile (20)
- Dyeing products (5)
- Masonry (1)
- Metal Work (11)
- Satsuma Suzuki: Satsuma Tinware
- Tosa Uchihamono: Tosa Blade
- Kaga Zougan: Kaga Inlay
- Akita Ginsen Zaiku: Akita Filigree
- Token: Japanese Sword
- Banshu-gama : Banshu Sickle
- Echigo-Sanjo Uchi Hamono: Echigo-Sanjo Blade
- Osaka Naniwa Suzuki: Pewter/Tin Ware
- Nakaniida-Uchihamono: Nakaniida Traditional Blade
- Higo-Tsuba
- Nokaji Hamono: Nokaji Blades
- Stationery (4)
- Livingware (3)
- Accessory (4)
- Toys & Entertainment (14)
- Interior (2)
- Other crafts (10)

![]() |
Main Production Site:Ishikawa |

Zougan (inlay) is a decoration technique to carve patterns on material such as metal, ware ceramic, or wood and etc., and insert gold, silver, and other materials into the carved parts there. Metal zougan is important as one of the metal-carving techniques and there are many zougan techniques including hira zougan (Japanese "hira" means flat and hira zougan is literally flat zougan; a method of making the surface of a zougan work flat after fitting metal into the model), which is the mainstream of "Kaga Zougan".
Beautiful and sophisticated patterns in Kaga zougan have an outstanding, keen feel for designs and such fine expression is supported by the minute methods. The craftsman carves the pattern part on the metallic basis material with a burin (tagane in Japanese), making the bottom wider than the surface (this method is called "ari wo kiru" in Japanese) and inserts and drives in a different metal in the part.
Then, the metallic part for the pattern is pressed and spread inside and does not come off itself. This bonding technology was closely employed especially in Kaga to enable to express variously on the metal for expressive work and gained a high reputation as for the solid work.
Of all the techniques, "Abumi" (stirrup) has been a synonym for Kaga zougan and well known for the scrupulous technique making sure that the metallic parts of Kaga zougan never come off, in addition to its excellent novel designs and gorgeousness.
[Traditional Craft Designated by Ishikawa Prefectural Governor]
Information provided by Kaga Zougan Tradition Research Laboratory, the Soukeikai Foundation
Translation by: Mie Nakajima, reviewed by Miwa Odagiri
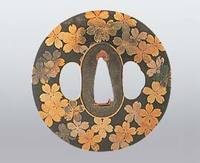
Materials | Sheet copper basis material, silver plate |
---|---|
Crafting Processes | 1. Sketch
Black sheet copper basis material is filed flat and smooth and a sketch is made on the sheet with a gauge or copying paper. Then, the outlines of the sketch are carved with a tagane. 2. Carving After carving the inside of the outline, carved parts areThe carved parts are made flat and smooth with a chisel called kisage after the surface inside the outlines is carved. 3. Driving With silver plate, the same patterns are made along to the shapes of the outlines and driven into the carved parts. 4. Zougan (Inlaying) The red copper is inlayed over the silver inlayed parts. The gold parts (legs) and copper parts (head) are inlayed. 5. Burnishing The whole plate is filed with the most delicate file (aburame yasuri) and then made flat and smooth on a whetstone. It is burnished with hard charcoal for burnishing (hozumi) and then mirror-finished with charcoal powder. 6. Color Development It is boiled in a solution of copper rust and copper sulfate to develop the color of each metal. |
History | Kaga zougan was originated at the end of the 16th century, when the Maedas, who had governed a feudal domain called Kaga, introduced its techniques from Kyoto region.
At the beginning, it was essential to create armor and harness with and had two types: various metallic fittings for sword decoration, and harness on which people riding a horse hang their feet (abumi or stirrup). In the domain, people with a distinguished skill were appointed to a craftsman artisans and their skills improved by the incentive measures gave a strong effect on craftsmen in the town, resulting in being in full flourish. Kaga zougan gained a reputation as Kaga's metalworking specialty. Nonetheless, it got in poor demand and many zougan craftsmen closed their business after the samurai society (society of warrior rule) collapsed. However, taking the opportunity of being displayed by the government in the International Exhibition in Vienna in 1873, Kaga zougan started to show its ability to produce big flower vases for export. It was taken over as a totally different style of plastic arts from what they used to be and survived. Koji Yamakawa the First, a famous craftsman in connection with the Soukeikai Foundation, was a successful master-hand as one of the leaders of Kaga zougan in such a difficult transition period. After World War II, in Kanazawa, there were few successors of Kaga zougan, which made the people fear that its techniques would not be taken over to the next generation. However, more and more young people have recently been involved in the zougan art. It has been expected that such artists will challenge zougan production which would be suited to the coming age and succeed in an innovative and various work of art. |
◆Exhibition / Showcase
Ishikawa Prefectural Museum of Art
Address: 2-1 Deba-cho, Kanazawa-shi, Ishikawa
Telephone: +81-(0)76-231-7580 (Japanese Only)
Opening hours: 9:30am-5:00pm (Entry before 4:30pm)
Ishikawa Prefectural Museum of History
Address: 3-1 Deba-cho, Kanazawa-shi, Ishikawa
Telephone: +81-(0)76-262-3236 (Japanese Only)
Opening hours: 9:00am-5:00pm (Entry before 4:30pm)
You can also see Kaga zougan at many other museums in Kanazawa.
Assistance needed? For inquiries in English:
JTCO Contact Form
Your inquiries will be forwarded by JTCO in Japanese to the organization you wish to contact.