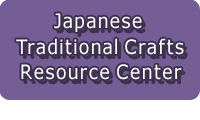
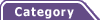
Total:131items
- Pottery & Porcelain (18)
- Koshu Kimen Gawara: Koshu Tile with a Devil’s Face
- Hasami Yaki: Hasami Porcelain
- Kiyomizu Yaki: Kyo style ceramics, Kiyomizu ware
- Otani Yaki: Otani Pottery
- Izushi Yaki: Izushi Porcelain
- Onta-yaki: Onta Pottery
- Takahama Yaki: Takahama Porcelain
- Mushiake- Yaki: Mushiake ware
- Kikuma-Gawara: Kikuma Roof-Tile
- Zeze-Yaki: Zeze ware
- TsutsumiYaki: Tsutsumi Pottery
- Hira Shimizu Yaki: Hira Shimizu Ware
- Tajima Banko Yaki: Tajima Banko Pottery
- Shidoro-Yaki: Shidoro Ware
- Amakusa Tojiki: Amakusa ware
- Shibukusa-yaki: Shibukusa ware
- Karatsu Yaki : Karatsu Ware
- Satsuma-yaki : Satsuma Ware
- Lacquerware (4)
- Glasswork (2)
- Wood & Bamboo Work (19)
- Leather Work (1)
- Papermaking (13)
- Textile (20)
- Dyeing products (5)
- Masonry (1)
- Metal Work (11)
- Stationery (4)
- Livingware (3)
- Accessory (4)
- Toys & Entertainment (14)
- Interior (2)
- Other crafts (10)

![]() |
Main Production Site:Miyagi |
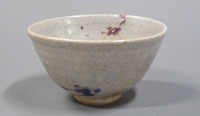
Tsutsumi Yaki is a sort of pottery made in Sendai, centered around simple everyday utensils such as dishes, pots, sake cups, sake bottles and tea cups. It is deeply involved with Sendai. It is made from the clay taken locally. The glaze is made from rocks and rice hull ash. It has a simple yet strong flavor.
It is notable for the rustic appearance derived from coarse local clay, as well as Namako-yu (black and white opaque glaze). Yanagi Muneyoshi, a philosopher and founder of the mingei (folk craft) movement in Japan, took notice of Tsutsumi Yaki as one of the most excellent kilns for folk craft in the Tohoku region, Northern Japan, and its water pots were especially highly regarded.
[Traditional craft designated by Miyagi Prefecture governor]
Source: Tsutsumiyaki Kenba kiln
Translation by: Satomi Hirasawa Yamashita, reviewed by Misaki Kobayashi
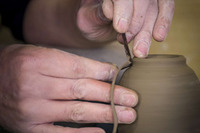
Materials | Clay, glaze, etc |
---|---|
Crafting Processes | [1] Clay making and Elutriation
Clay is transported from layers of clay in Dainohara, Miyagi Pref., and allowed to sit in a mound. Clay is scraped off the mound, softened with water and liquefied in a mixer. The liquid is passed through a sieve to remove branches, roots and stones, then placed in a water tank and allowed to precipitate over several months. Then water is removed, and the precipitated clay is placed in unglazed pots, and dried in shade for several days before being passed through a clay kneader and then left to age in a muro (chamber) for more than a year. [2] Wedging Aged clay is manually kneaded by skilled craftsmen to make the hardness uniform and to remove air making the clay tougher, and preventing cracks. [3] Shaping Shaping small products such as dishes and vases is done by a potter's wheel. Large products are made by bo-himo style, a process in which clay is formed into straight ropes (bo-himo) then piled on top of each other in rings. The shape is set by beating the sides with a board, with an assistant turning the potter's wheel. [4] Finishing After shaping the clay with wet hands, products are dried slowly for a couple of days. The foot is carved out when the pottery is half dry. It is inverted on a cylindrical pottery called "shitta", and trimmed with a plane and a bamboo pallet. [5] Drying Small products are dried for about one week. Big products are dried for more than a month in the drying chamber (muro) in order to prevent cracking [6] Biscuit firing Pottery is baked in a kiln at 800℃, in order to prevent deformation during glazing, and to allow glaze to better attach to the clay. [7] Glazing Glaze is applied to biscuit fired pottery. Main material for Namako-yu glaze, which is typical for Tsutsumi-yaki, is made from local rocks, rice husk ash and charcoal. [8] Glaze firing Pottery is fired in a kiln at approximately 1250℃. By firing glaze, it melts together with surface of clay to form glass, which prevents penetration of water and dirt. |
History | Tsutsumi-yaki started at Tsutsumi-cho (Aoba Ward, Sendai) in the late 17th century, during the Edo period. It is said that the initial producers were ashigarus (low-ranking foot soldiers) who were ordered to produce ceramics with the abundant, good quality local clay while assigned to live along the Oshu-kaido highway (the biggest road linking northern Japan to the rest of the country) so that they could serve as a defense force against the enemy from the north.
Tsutsumi Yaki was named after Tsutumi Town where its kilns were. At first, craftsmen made products for lords of Sendai who practiced Japanese tea ceremony. Subsequently, they started to make products for the common people's everyday utensils such as jars, bowls and dishes, and have inherited the technique for over 300 years to this day. There were 30 pottery makers at peak. Today, however, "Tsutsumiyaki Kenba Kiln" as the only remaining maker, continues to protect their tradition and technique in Marutazawa, Izumi Ward, Sendai. |
Related URL | http://tsutsumiyaki.net/ |
◆Exhibition / Showcase
Tsutsumiyaki Kenba Kiln
Opening Hours: 9:00-18:00
Exhibition/shop: Open everyday
Workshop: Closed on Sundays and National Holidays
Kamiya-gariaza-akasaka 8-4, Izumi-ku, Sendai-shi
Miyagi, 981-3121
TEL: +81-(0)22-372-3639
FAX: +81-(0)22-372-5829
(Japanese only)
Experimental workshops available (Japanese only - Reservation is required.)
Assistance needed? For inquiries in English:
JTCO Contact Form
Your inquiries will be forwarded by JTCO in Japanese to the organization you wish to contact.