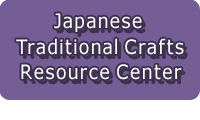
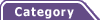
Total:131items
- Pottery & Porcelain (18)
- Lacquerware (4)
- Glasswork (2)
- Wood & Bamboo Work (19)
- Leather Work (1)
- Papermaking (13)
- Mino Washi: Mino Japanese Paper
- Ogawa Washi handmade paper
- Tegaki Koinobori (Hand-drawn Carp Streamer)
- Touzan-Washi: traditional Touzan Japanese Paper
- Sugihara-gami: Sugihara paper
- Najio-shi: Najio paper
- Nishinouchi Washi : Nishinouchi Japanese paper
- Yatsuo washi paper
- Yoshino Tesuki Washi: Yoshino Handmade Paper
- Gokayama Washi Paper
- Izumo Mingeishi: Izumo Folk Craft Paper
- Kurotani Washi: Kurotani Japanese paper
- Tosawashi:Handmade Japanese Paper
- Textile (20)
- Dyeing products (5)
- Masonry (1)
- Metal Work (11)
- Stationery (4)
- Livingware (3)
- Accessory (4)
- Toys & Entertainment (14)
- Interior (2)
- Other crafts (10)

![]() |
Main Production Site:Shimane |
The main characteristic of Izumo Mingeishi, Izumo Folk Craft Paper, is the technique which makes the most out of the texture of the material. All products are manufactured, enhancing the characters of different types of plant fibres. Whether it is made of kozo (paper mulberry) or gampi (Diplomorpha sikokiana), each sheet of paper has its own character, which is sometimes described as powerful or masculine.
There is a great variety, such as coloured paper and paper with colourful patterns. Some are used as materials for wood printing, others are used for postcards and business cards. The craftsmen employ different techniques depending on the use of the paper. Gampi paper is particularly suitable for important documents, since it is glossy and insect-repellent. Despite its soft texture, gampi paper is quite substantial and preserves well.
In 1968, the traditional papermaking technique using gampi is highly appreciated and awarded as an important intangible cultural asset. Izumo Mingeishi was named as a traditional craft officially designated by governor of Shimane prefecture in 1982.
[A Traditional Craft Officially Designated by Governor of Shimane Prefecture, and An Important Intangible Cultural Asset in Shimane Prefecture (Gampi paper)]
Contents provided by: Izumo Mingeishi Kobo
Translation by: Moe Shoji
Materials | Gampi, mitsumata, kozo(paper mulberry) and neri (made of sunset hibiscus) |
---|---|
Crafting Processes | 1. Cleaning the materials
The inner layer of white bark is soaked in the water for 24 hours and damaged parts are removed with knife. Normally three layers of white bark make a sheet of washi paper. About 4 tons of white bark is used every year among the craftsmen who manufacture Izumo Mingeishi. 2. Boiling the bark Cleaned white bark is boiled in a large pot with soda ash, until it gets soft. 3. Removing scum and small dusts Once the bark becomes soft enough, white bark is immersed in the clear water to completely remove the residue of soda ash. In order to make a paper with refined texture, any small unwanted debris is removed one by one by hand. 4. Breaking the ingredients The bark is beaten and broken into small pieces of fibre. This process used to be done by hand using a stick, but today it is done with a help of machinery. Depending on the type of the product, either a foot-powered stamper or a Hollander beater is used. The beaten fibre is called shiryo. When dying the paper, the beaten fibre is returned to the pot and cooked with a dye. 5. Kamisuki(Papermaking) The fibre is mixed in a vat with water and neri, or a sticky liquid extracted from the roots of Tororo Aoi (sunset hibiscus) plant. Once the mixture reaches the desirable stickiness, sheets of paper are made by scooping the solution with a set of papermaking utensils, a bamboo screen (Suki su) and a wooden frame (Suki keta). The technique used in Izumo Mingeshi is called “Nagashi suki”, which involves three steps: Kake-mizu, Choshi-mizu and Sute-mizu. These processes are similar to other Japanese papermaking, but the major difference in the technique of Izumo Mingeishi is the way the mixture of fibre and neri is adjusted and the method of handling utensils. In other papermaking techniques, they use quite a lot of neri and move the wooden frame back and forth to let any debris slide away at the final process of Sute-mizu. However, in Izumo Mingeishi they use less amount of neri and move the frame more slowly before draining the water. Sheets of paper are transferred to the pile while they are still wet. They do not get stuck with one another because of the function of neri. 6. Removing the moisture Newly made paper contains a lot of water. A stack of paper is tightly pressed to remove excessive moisture. 7. Drying Once excessive moisture is removed, sheets of paper are separated one by one from the stack for drying. There two methods for drying: sun drying and steam drying. In sun drying method, each sheet of paper is lined on a wooden board, while steam drying involves placing sheets of paper on a metal board. Either of the methods is chosen depending on the type of the final product. |
History | The history of papermaking in Izumo (current Shimane Pref., West Japan) dates back to Tempyo period (8c), although the technique was long forgotten since then until it was revived in Edo period (17-19c). It was in this era that the technique was greatly developed.
The advancement of papermaking in Izumo since Edo period (17-19c) was prompted by the first feudal lord of Matsue Domain, Naomasa Matsudaira. He invited the craftsmen from his hometown Echizen (current Fukui Pref., Central Japan) to establish a government-owned papermaking workshop in Noshira in the outskirts of Matsue. Since then, the feudal lord encouraged the cultivation of kozo, or paper mulberry, and handmade paper became one of the government monopoly goods of Izumo. Chikayoshi, the son of Naomasa, welcomed some of the papermaking craftsmen in Matsue to his domain, Ojidani Village, Hirose Town, Nogi District. This was in order to establish another government-owned papermaking workshop. The representative types of handmade paper in Izumo at that time include Noshira paper, Ojidani paper of Hirose, and Mabase paper of Nita. After the Meiji Restoration in 1868, papermaking in Izumo was rapidly developed since it was finally free from the control of Matsue Domain. In early Meiji period (19-20c), their Mugiwara paper (made from straw fibre) and Wara paper (made from rice fibre) became massively popular. However, this popularity unfortunately undermined the quality of the paper and the papermaking industry in Izumo gradually declined in the late Meiji period when the popularity was gone. There have been a couple of different stories around the papermaking in Bessho area in Izumo: some say that it inherits the refined and traditional technique of Noshira paper developed under the Matsue Domain; others say that it adapted the traditional technique to make it more affordable. Bessho area is located in a valley with little land to cultivate; therefore, people in this area traditionally practiced papermaking as subsidiary work to supplement their earning from farming. Bessho area long remained almost unknown as a place which produces a quality paper. Yet, they made efforts to establish Izumo Mingeishi, or Izumo Folk Craft Paper, in later years, by inviting experts from Tosa (current Kochi Pref., West Japan) in 1899 and 1900 to improve their technique and by creating a union to collectively purchase the raw materials for papermaking. Eishiro Abe was born on 14th January 1902 in Bessho, Iwasaka Village, Yatsuka District in Shimane Pref. (current Yakumo Town, Matsue City). Abe learned papermaking technique from early age by helping the family business. He worked for Papermaking Department of Shimane Pref. Industrial Laboratory and it is here that he improved his technique to the high quality, experimenting different papermaking approaches. Later, he became an instructor and traveled across Shimane Pref. to provide trainings to craftsmen. In 1931, Soetsu Yanagi, a philosopher who founded the Mingei (folk craft) movement, visited Matsue and saw gampi paper made by Abe. Yanagi highly praised his work, saying, "This is the very best of Japanese papermaking." Since then, Abe joined the Mingei movement. Abe's representative works include: Wasenshi, a dyed paper without undermining the texture of Japanese paper; Sukimoyogami, a paper with other fibre incorporated to create beautiful patterns; and Kizukigami, a paper only made out of a single type of vegetable fibre, such as kozo, mitsumata or gampi. Abe's papermaking started to be referred to as "Izumo Mingeishi (Izumo Folk Craft Paper)" and it became a niche craftwork loved by many fans across the country. |
Related URL | http://www.mable.ne.jp/~mingeishi/ |
◆Exhibition / Showcase
Izumo Mingeishi Kobo
Higashi-Iwasaka, Yakumo-cho, Matsue-shi, Shimane, 690-2102
TEL: +81 (0) 852-54-0303 (Japanese only)
Opening hours: 8:00 AM - 5:00 PM
Close on Sundays, National holidays, the New Year's and Obon; around August 15 (It could be closed on other days without notices.)
* There is no entrance fee for your visit to the workshop. Please contact us beforehand to make an appointment.
◆Event Information
Please check our web site for more information on exhibitions and events.
Click here for more info
Assistance needed? For inquiries in English:
JTCO Contact Form
Your inquiries will be forwarded by JTCO in Japanese to the organization you wish to contact.
*Please write the name of craft you wish to ask about.