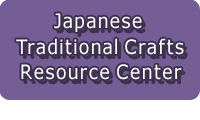
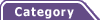
Total:131items
- Pottery & Porcelain (18)
- Lacquerware (4)
- Glasswork (2)
- Wood & Bamboo Work (19)
- Leather Work (1)
- Papermaking (13)
- Mino Washi: Mino Japanese Paper
- Ogawa Washi handmade paper
- Tegaki Koinobori (Hand-drawn Carp Streamer)
- Touzan-Washi: traditional Touzan Japanese Paper
- Sugihara-gami: Sugihara paper
- Najio-shi: Najio paper
- Nishinouchi Washi : Nishinouchi Japanese paper
- Yatsuo washi paper
- Yoshino Tesuki Washi: Yoshino Handmade Paper
- Gokayama Washi Paper
- Izumo Mingeishi: Izumo Folk Craft Paper
- Kurotani Washi: Kurotani Japanese paper
- Tosawashi:Handmade Japanese Paper
- Textile (20)
- Dyeing products (5)
- Masonry (1)
- Metal Work (11)
- Stationery (4)
- Livingware (3)
- Accessory (4)
- Toys & Entertainment (14)
- Interior (2)
- Other crafts (10)

![]() |
Main Production Site:Toyama |
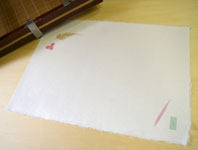
The main material for Gokayama paper is Gokayama Kozo (paper mulberry) which is grown in this area with abundant snow melt water. Kozo is famous for its long and strong fibers and have almost double length compared to Mistumata (paper bush) or Ganpi (diplomorpha sikokiana). Especially, Gokayama Washi contains much Kozo, thus it is guaranteed of its strength as paper. Also it has the features of warm and smooth touch due to the flexibility of its fibers.
Any chemicals are not used for breaching paper. The bleaching method called "Yuki-Sarashi" (Exposure to Snow) is used, which is peculiar in snowy region. Even today, Gokayama paper is hand-made by traditional method using natural materials, hardly depending on machines or chemicals.
While usual pulp paper turns yellow and deteriorates with time, . Gokayama paper keeps its durability,and we can not tell the difference between the paper crafted today and that of 100 years ago.. Consequently, the letters written with Indian ink back then on Gokayama paper has no color-fading and keeps their clearness even today.
Gokayama paper and other papers produced in Yatsuo or Asahi-machi, in Toyama Pref (Central Japan) are called "Ecchu-Washi". It is designated as one of the Nationally-Designated Traditional Crafts and its Japanese paper culture with long history and tradition fostered by the local nature, was revalued.
Today, Gokayama paper is an indispensable material for the repair of important cultural properties owed by Imperial Household Agency or the nation, such as Shoji (paper sliding door) for Katsura Detached Palace.
Also, Gokayama paper is a specially ordered item from artists for the material of various fine arts and crafts
such as Chigirie (Collage of pieces of colored paper), print art, painting and so on.
[Nationally Designated Traditional crafts (as Ecchu Washi)]
Information sources : Gokayama Washi no Sato
Translation by: Namiko Murakami
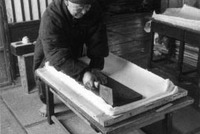
Materials | Gokayama-Kozo (paper mulberry), Tororoaoi (sunset hibiscus) |
---|---|
Crafting Processes | [1] Steaming Kozo
Kozo are cut into 1.2 meter in length, and steamed in the special barrel shaped steamer. [2] Beating Beating steamed barks by wooden hammer to peel the bark of Kozo easily [3] Peeling Kozo Peeling barks. [4] Drying Kozo Drying peeled barks under the sunlight for storage. [5] Scraping off black barks During the period of December to March, getting rid of black surface of barks manually. [6] Exposure to snow During the period of December to March, exposing barks to sunlight in the snow for 1 to 2 weeks. This removes chlorophyll from the barks, and naturally bleaches them. [7] Washing Kozo Washing away remaining black barks with fresh water. [8] Boiling Kozo Boiling Kozo barks with soda-ash in the caldron for 3 hours while stirring, then washing the scum away with running water after boiling [9] Cleaning Geting rid of dust from almost fibrous barks by hand. [10] Beating Beating the fibers to make them stronger. [11] Loosening fibers Loosening the fibers and make them pulpy. [12] Papermaking (Kamisuki) Water, fibers, and sticky liquid taken from the root of sunset hibiscus are mixed in Sukifune (papermaking tank) then disked by Sukiketa (deckle). Completed paper is taken out from Suki (wooden frame) and piled up one by one. [13] Compressing Getting rid of water from the paper slowly by pressing evenly. [14] Drying Attaching the paper to wooden boards to dry naturally. Sometimes using a steam-dryer. [15] Selecting Sorting out the paper by thickness or defects if any, to select only good quality paper. |
History | It is uncertain when papermaking started in Gokayama area. Gokayama used to be within the domain of Kaga, present Ishikawa Pref., Central Japan, in the feudal era. There found archives or records regarding Gokayama papermaking, as well as paper making tools such as Kaimisuki-bune (papermaking tanks made by hollowing out Japanese horse chestnut or Japanese zalkova), Takuri-bune (peeling tool for Kozo), boxes to contain ash used for boiling etc. It is an unprecedented case in Japan to find such rudimentary tools still remained.
Thus, it is presumed that papermaking method was directly introduced from Kyoto or Nara, both former capitals of Japan, then reformed into an particular method by the people in Gokayama village. In 1585, during the the feudal government era, , Gokayama paper along with other Gokayama products such as raw silk were offered as Nengu (an annual tribute, or land tax) to the domain lord. In addition, Gokayama paper was appointed as the domain's designated products as well as explosive powder to prevent technology leakage. In Gokayama village, each Gassho-zukuri household (wooden house with a steep rafter roof) would have a lot of hired people to produce explosive powder or Kozo in summer, and making paper (Kamisuki) in winter just like factory production line. After the World War 2, in 1950, Gokayama Paper Cooperative Association was established to protect the traditional Gokayama paper. In 1968, Higashi Nakae Paper Production Association was established to inherit its classical Japanese paper production method handed down from Edo-era conserving its traditional technique, while other Japanese papermaking sites disappear one after another. Under the circumstance that the demand for Japanese paper keeps decreasing due to the dominance of western paper made of pulp, In 1982, Japanese Traditional Paper Craft Research Center was established, which is the precursor of the current "Washi no Sato", the Japanese Paper Center in Gokayama. Until today, it develops new products and provides the education for the heirs. |
Related URL | http://gokayama-washinosato.com/ |
◆Exhibition / Showcase
"Michino Eki TAIRA" Gokayama Washi no Sato, (Japanese Paper Center in Gokayama)
Higashi nakae 215, Nanto-city, Toyama Pref. 939-1905
TEL: +81-(0)763-66-2223 (Japanese Only)
FAX: +81-(0)763-66-2250
Kamisuki (papermaking) experience available in Washi Experience Center
(Information provided only in Japanese)
Assistance needed? For inquiries in English:
JTCO Contact Form
Your inquiries will be forwarded by JTCO in Japanese to the organization you wish to contact.