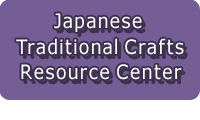
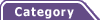
Total:131items
- Pottery & Porcelain (18)
- Lacquerware (4)
- Glasswork (2)
- Wood & Bamboo Work (19)
- Leather Work (1)
- Papermaking (13)
- Mino Washi: Mino Japanese Paper
- Ogawa Washi handmade paper
- Tegaki Koinobori (Hand-drawn Carp Streamer)
- Touzan-Washi: traditional Touzan Japanese Paper
- Sugihara-gami: Sugihara paper
- Najio-shi: Najio paper
- Nishinouchi Washi : Nishinouchi Japanese paper
- Yatsuo washi paper
- Yoshino Tesuki Washi: Yoshino Handmade Paper
- Gokayama Washi Paper
- Izumo Mingeishi: Izumo Folk Craft Paper
- Kurotani Washi: Kurotani Japanese paper
- Tosawashi:Handmade Japanese Paper
- Textile (20)
- Dyeing products (5)
- Masonry (1)
- Metal Work (11)
- Stationery (4)
- Livingware (3)
- Accessory (4)
- Toys & Entertainment (14)
- Interior (2)
- Other crafts (10)

![]() |
Main Production Site:Nara |
Yoshio Tesuki Washi, or Yoshino Handmade Paper, embraces the history of over thousand years, the natural environment of Yoshino and the pride of the craftsmen engaged in papermaking in the area.
Yoshino Handmade Paper has been loved because of its smoothness unique to Japanese paper, its soft quality, and the depth in its texture. It is widely used for artworks and beautiful interior decoration. Papers for filtering lacquer, which is the lifeblood of lacquering craft, are also made with Yoshino Handmade Paper. In other words, Yoshino Handmade Paper is one of the major elements which have played important roles to support Japanese traditional art and craft.
The secret of making papers of good quality is to soak the bark of kozo, or paper mulberry, in the very clear water in the wintertime.
It can be said that the clear stream of the Yoshino River has nurtured papermaking in Yoshino, even though its water quality is said to have deteriorated in recent years.
Variety of Japanese Paper
Udagami (Kuzugami) - is soft and resistant against insects, since it contains white clay. It also keeps the form nicely with its elasticity when rolled. It is often used as the backing paper of kakejiku, or a hanging scroll.
Misugami - is soft, as it is stuck on the board soon after being made (Subuse). The width of this paper is not affected by the change of humidity. It is essential to the mounting of a hanging scroll as the backing paper.
Yoshinogami - involves a process called Subuse like Misugami. Thin and fine in texture. It is essential to lacquer filtering.
Yoshino-sugikawa-washi - Yoshino takes pride in its nationally famous brand of timber, "Yoshinozai", or cedar trees produced in Yoshino. This paper was born from an idea to make the most of the bark of this acclaimed cedar, which ends up being disposed after sawing.
This paper is equipped with a unique hue of warmth and a smooth texture, thanks to the mixture of inner bark of Yoshino cedar and kozo.
Kusakizome-washi - This paper is made with a mixture of kozo or paper mulberry, a main ingredient for Japanese paper, and the boiled bark of cherry tree, akebi, silk tree, tomato plants, mugwort, Chinese indigo, and Cleyera japonica.
[Traditional Craft Officially Designated by Governor of Nara Prefecture]
Information & materials provided by: Fukunishi Washi Honpo
Translation by: Hiroko Okamura, reviewed by Moe Shoji
Materials | Kozo or Paper Mulberry |
---|---|
Crafting Processes | It is generally said that Japanese papermaking involves 48 individual processes. It is a considerable hard work to make Japanese paper as it is mainly done at the coldest time of the year, using the very cold water.
1. Harvesting kozo Cut down kozo from the field and trim them into the same length (1.2 m). 2. Steaming kozo (Steaming raw timber) Steam the kozo for approximately 4 hours. 3. Barking kozo Bark the steamed raw timber. This raw bark is called "kuroso" (black kozo). 4. Ripping dark epidermis Remove the epidermis from the kozo bark. This remaining material is called "shiroso" (white kozo). 5. Sun drying Once the bark is made into "shiroso", it is preserved for two years, drying them in the sun from time to time, in order to make the texture of fiber tighter. 6. Soaking (Rinsing shiroso or steeping kozo) Expose (*1) a bundle of shiroso in the Yoshino River, leaving the top open in a shape of flower petals. They are soaked on a sunny day, for 8 hours in winter and for 4 hours in summer. 7. Cutting dust away Cut away the damaged parts of shiroso with a razor. 8. Boiling shiroso Slowly boil shiroso in the lye of trees and plants (*2 Somoku-aku). The lye is sometimes replaced by soda ash. 9. Washing in the water (Take out shiroso or the paper material) Wash away the lye of trees and plants. 10. Removing dust Carefully remove any dust from shiroso. 11. Beating shiroso Beat shiroso little by little (*3 Hoso-uchi) with two pieces of oak stick on the top of the stone base. 12. Fibrillate shiroso fiber (*4 Zaburi-kake) Add the neri (*5) and white clay to the shiroso and stir well with a tool called "zaburi". 13. Tesuki (Papermaking) Manually produce a paper very carefully to keep an even thickness. 14. Compressing "shito (paper bed)" (Dehydration of Kamidana *6) Dehydrate the sheets of moist paper by compressing them. Once the papers are dry, they are sorted and shipped. [Notes] *1 Expose - A process to harden the fiber properly as well as rinsing in the running water. *2 Lye of trees and plants (Somoku-aku) - The ash is mainly from hard timbers, such as evergreen oak and Japanese chestnut oak. *3 Beat little by little (Hosouchi) - A process to soften the fiber and produce fine texture and tenacity. *4 Zaburi - A wooden tool to refine the fiber and to stir it well. *5 Neri - An ingredient made from finely chopped bark of deutzia tree. *6 Kamidana - Also called "shito (paper bed)". The freshly made papers piled up to strain the water. |
History | It is said that the origin of Yoshino Handmade Paper dates back to the 7th century, when Prince Oama first brought papermaking skills together with silk-raising to a village in Kuzu region of Yoshino.
Up until the mid-Meiji period (19 - 20c), the main material of Japanese paper, kozo or paper mulberry, was grown mainly in Kuzu region, where nearly a half of households were engaged in papermaking. Despite the decrease in demand after the World War II, high-quality Japanese paper with fine texture and tenacity has gained its popularity in recent years. Kozo being exposed in the clear water and sheets of carefully made Japanese paper dried in the garden are the poetic features of this area in winter months. Yoshino Handmade Paper is still produced in the traditional method and the warmth of its texture softens our hearts. The keys to produce papers of good quality are the unpolluted air and the clear water. In that sense, Yoshino is a village particularly suitable for papermaking. |
Related URL | http://kuzunosato.jp/syoukai/index.html |
◆Exhibition / Showcase
Monozukuri Taiken Kobo (Handmade workshop) at Kuzu no Sato
(In Japanese)
Assistance needed? For inquiries in English:
JTCO Contact Form
Your inquiries will be forwarded by JTCO in Japanese to the organization you wish to contact.