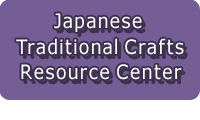
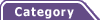
Total:131items
- Pottery & Porcelain (18)
- Lacquerware (4)
- Glasswork (2)
- Wood & Bamboo Work (19)
- Leather Work (1)
- Papermaking (13)
- Mino Washi: Mino Japanese Paper
- Ogawa Washi handmade paper
- Tegaki Koinobori (Hand-drawn Carp Streamer)
- Touzan-Washi: traditional Touzan Japanese Paper
- Sugihara-gami: Sugihara paper
- Najio-shi: Najio paper
- Nishinouchi Washi : Nishinouchi Japanese paper
- Yatsuo washi paper
- Yoshino Tesuki Washi: Yoshino Handmade Paper
- Gokayama Washi Paper
- Izumo Mingeishi: Izumo Folk Craft Paper
- Kurotani Washi: Kurotani Japanese paper
- Tosawashi:Handmade Japanese Paper
- Textile (20)
- Dyeing products (5)
- Masonry (1)
- Metal Work (11)
- Stationery (4)
- Livingware (3)
- Accessory (4)
- Toys & Entertainment (14)
- Interior (2)
- Other crafts (10)

![]() |
Main Production Site:Toyama |
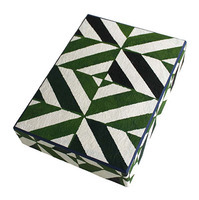
Yastuo-machi is a town full of natural beauty. Long ago, it was a bustling business center located along the trade routes of the time. Trade with merchants from the adjacent Hida area (current Northern Gifu Prefecture in Central Japan), along with various local businesses brought prosperity to the town. These included silkworm farming, producing and selling of medicinal items, and of course, Yatsuo washi paper. Handmade in this town, Yatsuo washi has not traditionally been produced as paper to write on; rather, it has been crafted and developed as a base material for creating other products, such as sachets and carrier cases used in the medicinal products vending of the region.
During Yatstuo-matchi's most productive period back in the early Meiji Era (19th-20th century), many families made washi paper to earn a living during the cold winter when farming was suspended. There was even a common saying: "There is no family among the thousand in Yatsuo that does not make paper."
Handmade washi paper is generally thought to be delicate and easily torn. Washi paper made in the Ecchu (Central Japan) area, including Yatsuo washi, has set itself apart by being so durable that it can function as a base material to make other paper products.
The age-old papermaking tradition of Yatsuo washi has been preserved and passed on to today’s artisans, and long-lasting paper products made from it are appreciated and enjoyed by many.
[Ecchu washi is designated as "Traditional Craft Product" by Japanese Ministry of Economy, Trade and Industry]
Information provided by Keijusha
Translation by: Misa Imanaka-Miller
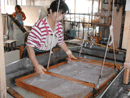
Materials | Paper mulberry, edgeworthia, gampi barks |
---|---|
Crafting Processes | 1) Maceration
Soak in water and macerate the dried bark from trees such as paper mulberry, edgeworth, and gampi. 2) Boiling Boil the bark in caustic soda (sodium hydroxide) or soda ash solution for two hours. 3) Washing and bleaching Wash the boiled bark in clean water as many times as needed to reach the desired brightness. Washing removes alkaline residues as well as unwanted matter, including non-hemicellulose materials such as lignin and pectin. Bleaching agents can be added if necessary. 4) Cleaning While keeping the bark under water, remove dirt, specks and other imperfections by hand. 5) Beating Beat the bark and separate the fibers to make the pulp. 6) Pulling sheet In a vat, mix water, pulp and "neri" (a mucilaginous material extracted from taro roots) into a slurry. This helps the fibers to distribute evenly in the water. Using a screen laid in a deckle, scoop the slurry and shake it back and forth to coalesce the fibers into a sheet. Place the freshly made paper sheets (shito) one by one to make up a pile. 7) Pressing Remove water from the sheets by pressing the pile. 8) Drying Peel the pressed sheets one by one and dry them on a flat surface such as a metal or wooden board. 9) Quality check Each sheet is carefully examined for its quality. |
History | Papermaking in Yatsuo peaked between 1688 and 1704 in the Genroku Era, when the 2nd Domain Lord of Toyama, Masatoshi Maeda, took an active role in encouraging medicine vending throughout the area. His actions caused dramatic growth and a huge demand for paper products used in the medicinal businesses in the area, such as medicine sachets, ointment paper, thin paper strips for binding, and logbooks used in record-keeping.
According to a wholesale paper pricing handbook published in the first year of the Keio era (1865) by a paper merchant in Toyama, Yatsuo paper was available in various colors including grey, yellow, red, and blue. This indicates the dyeing technique in this area was utilizing plants and other pigments, and was quite advanced for the time. These techniques are still being used in Yatsuo washi papermaking, and the area still produces the largest amount of hand made paper in Japan. |
Related URL | http://www.keijusha.com/ |
◆Exhibition / Showcase
Keijusha
668-4 Kagami-machi, Yatsuo-cho,
Toyma City, 939-2341, Japan
TEL +81-(0)76-455-1184 (Japanese only)
FAX +81-(0)76-455-1189
Washi papers are in display at Keijusha's paper mill; "Washi Bunko". Papermaking workshops are also available at the mill.
Hours: 10:00 - 17:00 (Door closes at 16:30)
Closed: Mondays (Tuesday, when a holiday falls on a Monday), 9/5, 9/6, 12/29-1/10
Admission: 500 yen (Free if only visiting the gift shop or the coffee shop.)
Papermaking workshop fee: 500 yen
More info at http://www.keijusha.com/kamisuki.html (in Japanese).
Assistance needed? For inquiries in English:
JTCO Contact Form
Your inquiries will be forwarded by JTCO in Japanese to the organization you wish to contact.