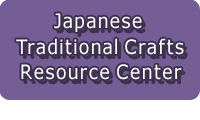
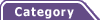
Total:131items
- Pottery & Porcelain (18)
- Koshu Kimen Gawara: Koshu Tile with a Devil’s Face
- Hasami Yaki: Hasami Porcelain
- Kiyomizu Yaki: Kyo style ceramics, Kiyomizu ware
- Otani Yaki: Otani Pottery
- Izushi Yaki: Izushi Porcelain
- Onta-yaki: Onta Pottery
- Takahama Yaki: Takahama Porcelain
- Mushiake- Yaki: Mushiake ware
- Kikuma-Gawara: Kikuma Roof-Tile
- Zeze-Yaki: Zeze ware
- TsutsumiYaki: Tsutsumi Pottery
- Hira Shimizu Yaki: Hira Shimizu Ware
- Tajima Banko Yaki: Tajima Banko Pottery
- Shidoro-Yaki: Shidoro Ware
- Amakusa Tojiki: Amakusa ware
- Shibukusa-yaki: Shibukusa ware
- Karatsu Yaki : Karatsu Ware
- Satsuma-yaki : Satsuma Ware
- Lacquerware (4)
- Glasswork (2)
- Wood & Bamboo Work (19)
- Leather Work (1)
- Papermaking (13)
- Textile (20)
- Dyeing products (5)
- Masonry (1)
- Metal Work (11)
- Stationery (4)
- Livingware (3)
- Accessory (4)
- Toys & Entertainment (14)
- Interior (2)
- Other crafts (10)

![]() |
Main Production Site:Ehime |
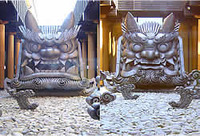
Kikuma-Gawara, among other roof materials, has distinctive features as following:
*Kawara is a traditional Japanese tile roof, a general noun; and the top "K" sound is replaced by "G" in this case for a proper noun, Kikuma-"G"awara.
BEAUTY; the peculiar beauty of the oxidized silver color enables various types of expression and appearance with the material covering all over the roof is graceful.
DURABILITY; it is firm and durable, and exceedingly tough.
WATERPROOF; it is incredible in waterproof with less water absorbency and rich water drainage function.
TEMPRETURE CONTROL; it keeps the inside cool in summer and warm in winter
REASONABLE PRICE; since it is a traditional material which fits the Japanese weather, it holds long with a reasonable price
[Designated Traditional Specialty of Ehime Pref.]
Sponsored by: Cooperative Association of Ceramics in Kikuma-City
Translation by: Aya Matsui, reviewed by Marina Izumi
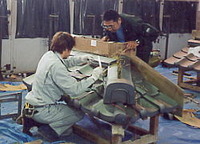
Materials | Clay (of Sanuki and Gomi) |
---|---|
Crafting Processes | Kikuma-Gawara, manufactured under the process of traditional techniques joined by modern technology and facilities, finally shipped as products after closely examined. The major manufacturing process of Kikuma-Gawara is as below.
1. Mining the Original Soil Kikuma-Gawara, composed of 60% of Sanuki-clay and 40% of Gomi-clay that is mined within the city, is made with the suitable fine qualified clay that is carefully selected. 2. Blending the Soil Each of the original clay has different contents and the ratio of water included; in this process, both of the clays are crushed into pieces and blended with a proper quantity of moisture. 3. Letting the Clay Stand Within the blended clay, each kind of clay is still full of their distinctive sharpness that distracts the harmony and stability of the blend; thus in order to make an arrangement, this process called "killing," with letting the clay stand for 10 days covered by a clothe, literary kills the sharpness and follows stability of the condition of the clay. 4. Molding of Rough Clay The original blended clay is evacuated in a machine still more, and at last, molded into a shape of Kawara, the Japanese tile roof. The original clay is called Araji or Soji, and the respective region's cooperative association of ceramics produces it, and delivers to each office of the region. 5. Press Molding Delivered clay is let stand for 4 to 10 days at the factory again, and put into the pressing machine that molds the clay into each shape of tiles. For those unique shapes of tiles, since they cannot be molded on a machine, craftsmen mold the clay by hand. In fact, it is one of the distinctive features of Kikuma-Gawara in that it is handmade by a sophisticated craftsmen with their special techniques. 6. Polishing The molded clay is finished with isinglass; and this process is called "Migaki (polishing)" in which the molded clay is re-processed on its surface. In the course of drying itself, molded clay is apt to warp; accordingly, "migaki" protects the clay from distortion and emphasizes the brightness on the surface. Needless to say, this traditional technique by hand is another unique feature of Kikuma-Gawara. 7. Drying The polished tile is shade-dried for roughly 5 days; this process is to decrease distortion. Since abrupt drying causes deterioration, it is ideal to dehydrate the tile in a condition as natural as possible such as to dry in the remaining heat of the kiln. Now, the properly dehydrated tile is called "Shiroji"; and apply cover coat on this "Shiroji" that is to be fired in the kilt. 8. Calcination The tiles are burnt in the modern technique of gas-fired kiln; using butane as the fuel, 1000 to 1500 tiles are burnt in a kiln at a time. They are burnt at a temperature in a range of 1000 to 1050℃and then, closed up tight for smoking for almost 20 hours. The silver brightness is marked on the tiles in this process, and it is also a moment when the traditional technique comes to life. 9. Inspection and Forwarding The finished tiles are closely inspected one by one. After passing the tests which examine the hardness, the size, the curves, the smoked color, and water absorbency, the uniform products are shipped. For the qualified Kikuma-Gawara, Ehime Pref. designates them as the traditional products and guarantees the qualification. In the Edo period (17-19c), the roof-tile was used in building Matsuyama castle; also in Meiji period (19-20c), it was used in building the Imperial Palace with blessing for the prosperity; moreover, nowadays, the roof-tile is not just for official or religious buildings.It enriches local people's lives, protects the roofs of Japanese buildings and hands down the beauty of Japanese architecture to the present. 10. The Product There are roughly 50 kinds of roof-tiles in the Japanese style that protect the roofs. The basic tile is called Zigawara, literally meaning the roof-tile of the ground; for the tile for specific use is called Yakugawara, meaning the roof-tile of a role; and the symbolic tile of the roof is called Onigawara, meaning the roof-tile of demon. Kawaras are distinctively different in the sizes depending on where they are from and their usage; speaking of Kikuma, its size is said to be the best size to make the roof look beautiful. |
History | Kikuma Gawara has its history of 750 years.
In 1278, the roof-tile was offered to Kono lineage in building the family castle In 1573, under the process of building the Azuchi Castle, techniques using wooden model was handed down by a high ranking priest In 1604, Kikuma Gawara was offered in building of Matsumae Castle and Katsuyama Castle by Yoshiaki Kato In 1818, the Kawara was offered to repair the Imperial Palace in Kyoto, West Japan In 1828, the Kawara was used in building the Osaka Residence of the Matsuyama domain In 1831, a pair of lantern made of Kawara was offered to Ko-Shrine In 1845, the Kawara was offered to Oyamazumi-Shrine In 1854, the Kawara was offered to repair Matsuyama Castle In 1855, the Kawara was offered to the Edo Residence of the Matsuyama domain In 1867, the Kawara was offered to the residence of Hiroshima domain In 1883, the Kawara was offered to the Imperial Palace In 1898, the Kawara was offered to the Residence of Count Hisamatsu in Matsuyama, West Japan In 1928, a cooperative limited liability company of Kikuma-Gawara was founded In 1939, the industrial guild of Kikuma-Gawara was founded In 1942, the industrial guild of Kawara in Ehime was established In 1943, a fighter aboard a warship "Ehime Kawara" was offered In 1978, O-oni-Gawara, a large symbolic tile, was offered to Henjoin, a temple, for protective charm In 1979, a laboratory for qualifying Kawara was founded In 1980, Cooperative Association of Ceramics in Kikuma-City was established and Kikuma-Gawara was designated as the traditional product of Ehime Pref. In 1982, a huge wall painting of Kawara in the Kikuma Civic Hall In 1993, the event called "Beloved Kikuma City '93" took place In 1997, the Homeland of Kawara Park & the Kawara Hall were built In 2002, the roof kawara was used in building the Martial Art Stadium of Ehime In 2007, the trademark of "Kikuma-Gawara" was obtained by the region |
Related URL | https://kikumakawara.com/ |
◆Exhibition / Showcase
Kawara-Kan
Postal Code: 799-2303 Kikuma Town 3067, Imabari City, Ehime Pref.
TEL:+81(0)898-54-5755
FAX:+81(0)898-54-5754
(Japanese Only)
Fee: adult (200yen), students under 18(100yen)
* A group discount is offered
Open: 9:00-17:00
Closed: Monday (If Monday falls on a Japanese holiday, the next day is closed)
Assistance needed? For inquiries in English:
JTCO Contact Form
Your inquiries will be forwarded by JTCO in Japanese to the organization you wish to contact.