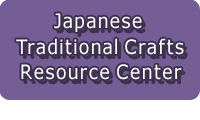
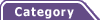
Total:131items
- Pottery & Porcelain (18)
- Lacquerware (4)
- Glasswork (2)
- Wood & Bamboo Work (19)
- Hakone Yosegi Zaiku: Hakone Marquetry
- Boshu Uchiwa: Boshu Fans
- Nikko-bori: Nikko carving
- Sasebo Koma (Sasebo Spinning Top)
- Shimoda Yanimatsu Zaiku (Shimoda Joinery of Oily Pine)
- Echizen Takeningyo (Bamboo Dolls)
- Osaka Senshu Kiri-dansu: Paulownia chest of drawers or wardrobes of Senshu, Osaka
- Kitayama Maruta: Japanese cedar logs
- Yodoegasa: Yodoe umbrella
- Atami Kusu Zaiku: Atami Camphor wood crafts
- Kawatsura Kokeshi Doll
- Itaya Zaiku: Itaya Bark Craft
- Yokohama Classic Furniture
- Hinaga Uchiwa: Hinaga Fan
- Torafu Takezaiku: Tiger Bamboo Work
- Tsuruzaiku: Woven Vine Craft
- Okawa Kumiko: Okawa Kumiko Wood Joinery
- Shuro Houki: Hemp-palm Broom
- Furyumen: Wood Carving Mask
- Leather Work (1)
- Papermaking (13)
- Textile (20)
- Dyeing products (5)
- Masonry (1)
- Metal Work (11)
- Stationery (4)
- Livingware (3)
- Accessory (4)
- Toys & Entertainment (14)
- Interior (2)
- Other crafts (10)

![]() |
Main Production Site:Mie |
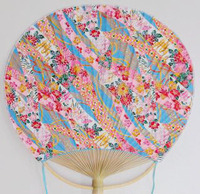
As you can see on the mural of Takamatsuzuka tomb (Asuka Village, Nara Pref.), fan has been used as a protection against wind, sunlight and dust, and also as accessories to hide face. Fan came to Japan from China via Korea and the nobles in Nara period (8c) started using the fan. In Sengoku (Civil Wars) period (15-16c), fan was also used as a commanding tool by military leaders.
Hand-made bamboo fans are categorized into three categories; "Hirae (flat handle)", "Sashie (grip handle)" and "Marue (rounded-handle)" by their handle feature.
"Hirae" is the fan with a flat handle which is made by cutting and planing a big bamboo. The "Hirae" fan is mainly produced in Marukame of Shikoku region (West Japan).
"Sashie" is a fan that a fan plate and a handle are made separately. Thin ribs are arranged at radiate pattern then the handle is attached to the fan plate. The "Sashie" fans are mainly produced in Kyoto.
The last one is "Marue" fan which uses a round bamboo as it is. Hinaga-uchiwa is categorized as the "Marue" fan (cut bamboo fan). Pursuing the user-friendly handle, the firm and highly elastic Hinaga-uchiwa was produced.
A thin bamboo is made into the rounded-handle which perfectly fits a palm and allows users to feel comfortable, cool and pleasant when holding it. Simon Bamboo, which is used for fishing rods as well, is finely cut and the bamboo ribs are woven alternately into bag- shape so that the fan bend beautifully like a bow.
It is difficult to form a three-dimensional bamboo into a flat fan and requires high skills. However, this is the key to bring the fan an elegance feature that makes the breeze blowing off the fan gentle and pleasant.
"How to create a comfortable wind?" is a question repeatedly asked in manufacturing the fan because "wind" is a life of a fan. Hinaga-uchiwa which sticks to the cut bamboo has been preserved as a tradition for 300 years up until today.Nowadays, the fan manufacturing keeps changing to meet the current needs while keeping its tradition. Various kinds of fan have been designed and made such as a fan with a long handle which is easy to insert between kimono and sash at festival, a fan with a flute, a cloth-made fan, a deodorant fan and a mosquito repellent fan.
[Mie Prefecture Designated Traditional Craft]
Information provided by: Inatoh Co., Ltd.
Translation by: Chan Yee Ting, reviewed by Marie Mine
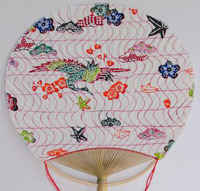
Materials | Bamboo, Japanese paper, etc |
---|---|
Crafting Processes | [1] Sawing bamboo
Saw a long bamboo in fan size. [2] Soaking the bamboo in water overnight Soak the bamboo in water and soften to be easily processed into ribs . [3] Cutting the bamboo Cut the rounded-handle into half till the bamboo joint then cut each half into 32 ribs making 64 ribs in total. [4] Standing the bamboo for a while Let the bamboo stand for a while to be processed easily later on. [5] Weaving the ribs with threads Weave the 64 ribs alternately with threads. [6] Installing a fan framework Attach a bow-shaped bamboo and tie it to the framework with threads. The framework is completed. [7] Cutting paper Cut patterned paper for the fan plate and "ear" paper along a fan pattern. [8] Pasting the paper Glue the paper on the bamboo. Once the bamboo is sandwiched in the paper, press the fan and dry it. [9] Cutting off the paper Cut off the unnecessary parts of the paper below the bow-shaped bamboo. [10] Die cutting Cut the fan into a full-moon/egg shape with a special tool. [11] Edging Edge the fan with long thin paper strips to prevent the patterned paper from peeling off easily from the edge of the fan. [12] Pasting the "ear" paper Paste the "ear" paper on the border between the ribs and the patterned paper on both sides. [13] Making the ribs stand out Press the fan with a roller to make the ribs stand out from the patterned paper. The fan is completed with this process. |
History | Originally, fan came from China and the nobility and powerful families used the fan as accessories and protection against dust, wind and sunlight. It was the Edo period (17-19c) when the fan started to be commonly used by general people as well.
During the Edo period, "Hinaga-uchiwa (fan)", "Naga-mochi (rice cake)" and "Hinaga-tabi (Japanese socks)" were sold as the top three special souvenirs from the Hinaga post town on the road from Kyoto to Edo. The "Hinaga-uchiwa" manufacturing is said to have started around 300 years ago. There were a lot of good quality bamboos growing wild at the riverside of the Tenpakugawa river and the Kabakegawa river and farmers are believed to have started the fan making using these bamboos during the agricultural off-season. The fan was popular as the souvenir from the Ise pilgrimage. On the way of their Ise pilgrimage, people ordered their favourite pattern for a fan and picked up the finished Hinaga-uchiwa to take it home with them thus the Hinaga-uchiwa spread all over Japan. The highway was flourished with over 10 manufactures and many souvenir shops. |
Related URL | http://www.inatoh.co.jp/ |
◆Exhibition / Showcase
Inatoh Yokkaichi
Opening Hours: 10:00-19:00
(Close on the Bon festival and New year's day)
4-4-48, Hinaga, Yokkaichishi, Mie Prefecture, 511-0885
TEL: +81-(0)59-345-1710 FAX: +81-(0)59-347-1379
(Japanese Only)
Assistance needed? For inquiries in English:
JTCO Contact Form
Your inquiries will be forwarded by JTCO in Japanese to the organization you wish to contact.