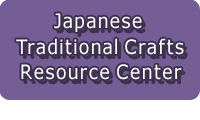
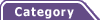
Total:131items
- Pottery & Porcelain (18)
- Lacquerware (4)
- Glasswork (2)
- Wood & Bamboo Work (19)
- Leather Work (1)
- Papermaking (13)
- Mino Washi: Mino Japanese Paper
- Ogawa Washi handmade paper
- Tegaki Koinobori (Hand-drawn Carp Streamer)
- Touzan-Washi: traditional Touzan Japanese Paper
- Sugihara-gami: Sugihara paper
- Najio-shi: Najio paper
- Nishinouchi Washi : Nishinouchi Japanese paper
- Yatsuo washi paper
- Yoshino Tesuki Washi: Yoshino Handmade Paper
- Gokayama Washi Paper
- Izumo Mingeishi: Izumo Folk Craft Paper
- Kurotani Washi: Kurotani Japanese paper
- Tosawashi:Handmade Japanese Paper
- Textile (20)
- Dyeing products (5)
- Masonry (1)
- Metal Work (11)
- Stationery (4)
- Livingware (3)
- Accessory (4)
- Toys & Entertainment (14)
- Interior (2)
- Other crafts (10)

![]() |
Main Production Site:Hyogo |
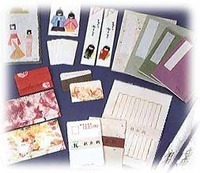
The greatest characteristic of Sugihara-gami is its whiteness. While there are some bleached white paper today, Sugihara-gami has more natural whiteness compared to those produced in other places. The black color of “Sumi”, the ink for calligraphy stands out, if you write letters with it on Sugihara-gami.
To create this whiteness, craftsmen never fail to perform a process of Kawasarasi (washing paper in the river for bleaching) in winter. Its fluffiness is another characteristic of Sugihara-gami; Its processed products are very soft to the touch.
[A designated traditional craft by Hyogo Pref.]
Provided by Sugihara-gami Kenkyujo (Sugihara Paper Laboratory)
Translation by: Mana Hara, reviewed by Marina Izumi
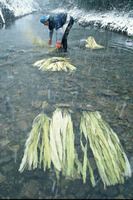
Materials | Kozo (Paper mulberry) |
---|---|
Crafting Processes | 1. Kozo-gari (Kozo cutting)
Kozo, which is the raw wood of Sugihara-gami, grows several buds from stumps in spring and grows 2-3m in autumn. Cutting and arranging Kozo after there are some frost and falling leaves. 2. Kozo-mushi (Kozo steaming) Steaming Kozoarranged to 1.2m with a big kettle to strip it off. 3. Kawahagi (Peeling) Peeling the bark of steamed Kozo while it is hot. 4. Kozo-momi (Kozo crumpling) Crumpling and softening the peeled bark with feet for easy shaving of the crust. 5. Kurokawa-tori (Getting rid of black bark) Shaving the crust of black bark with knife to turn it into white bark. 6. Kawasarasi (Soaking in river) Soaking the white bark in Sugihara river for one night and whitening it by bleaching in snow and cold water. The colder the outside air is, the more whiteness the white bark gets . 7. Kizutori (Removing bad fibers) Saving only beautiful fiber for paper of good quality by removing tiny pieces of chip. 8. Kamadaki (Boiling in cauldron) Soaking the white bark with clean water for one night, adding soda ash to this in a cauldron and then boil it so that impurities around fiber are dissolved in water easily. 9. Kozo-midashi (Removing dusts) Ridding of "dusts" after removing impurities of boiled bark of Kozo with clear stream. This work is so hard to the extent that hands get cut with coldness in winter. However, a really high quality paper is brought about from this hard work. 10. Kami-tataki (Beating paper) Beating paper materials with machine (mortar) to loosen fiber, while a wooden hammer used to be used in old days. In addition, breaking down the fibers with beater (machine with sickle). 11. Kami-suki (Spreading paper) Adding and stirring beaten paper materials and Sana (glue made of root in sunset hibiscus) well in a water-filled tank. Making paper one by one by shaking Suketa, the papermaking screen and deckle. There are three processes here, 1. Kesho-mizu (spreading the fibers evenly on the screen) , 2. Choshi (shaking the deckle so that the fibers tangle well) and 3. Sutemizu (draining water), to make a sheet of paper. When finished, taking the screen off the deckle then piling up the wet paper up to 150-200 sheets on paper bed. 12. Compressing Leaving the paper for a night and compressing it with a jack the next morning. This process of compressing needs to be done slowly. 13. Drying paper Stripping compressing paper one by one and, drying it by sunlight after putting it on drying boards with a brush. Today, using an iron plate is the main drying method from the viewpoint of unseasonable weather and efficiency. 14. Selecting Not all the completed paper is sold as a product. The finished paper are carefully inspected one by one and only those passed this inspection are sold as merchandise. |
History | It is assumed that paper production started in Sugihara valley of the northern part of Kami word, Taka town in the latter half of the 7th century. Sugihara-gami was called "Harima-gami" in Nara period (8c) and made as a paper for hand-copying of sutra and flimsy mainly. There were nearly 20 provinces which made paper in the whole country in this period.
However, the following record says that Harima (current Hyogo Pref., West Japan) was known for an advanced province of papermaking that competed with Izumo (current Shimane Pref., West Japan), Mimasaka (current Okayama Pref., West Japan), Mino (current Gifu Pref., Central Japan), Echizen (current Fukui Pref., central Japan) and Owari (current Aichi Pref., Central Japan), and accepted orders for 10,000 sheets of paper in Tempyo 16 (744) and orders for 17,000 in Tempyo 18 (746). In addition, there is a following description that clarified the excellence of Harima-gami in the paper's study report in Shosoin (The Treasure House in Nara) which was carried out in Showa 35 or 36 (1960,1961). The paper used for "Harimakoku Shozei Cho (Harima province settlement of accounts for tax)" which Harima provincial governor submitted in Tempyo 18 (746) was much progressing with technique than the paper of Izumo. Further, there is a record that Harima flimsy 40 quires were included in the gift which was taken by a monk of To-ji Temple who was sent to Seiryu-ji Temple of Chang'an (current Xi'an, North central China), Tang in Jowa 3 (836). It is indicated that Harima was prized as the best paper in Japan both in name and in reality in those days. Harima-gami came to be called Sugihara-gami since Heian period (8-12c). Then regent Fujiwarano Tadazane wrote in his diary, "Denryaku", that he had presented Yasuko (his daughter) and Tadamichi (his oldest son, then Lord Keeper of the Privy Seal) with 100 quires of "Sugihara-shonokami (椙原庄紙, paper made at Sugihara manor)" in addition to the family treasure of the Fujiwara family as “Hikidemono”, a gift of Buddhist service of their ancestors on 11th July Eikyu 4 (1116). “Denryaku” is the first document confirmed at present which indicated a name of Sugihara-shounokami. The name is assumed to have been originated in the later half of the 11th century when this place was the manor of Fujiwara clan. This paper, which was used by only the Fujiwara family at first, came to be cherished by many people. The letter used for Sugihara-shonokami (椙原庄紙) changed from "椙" to "杉" (both stand for cedar, but the former is the old letter), then the name was abbreviated as Sugihara (杉原) and called by a variety of names (such as Sugihara, Suibara, Suihara) from the end of Heian period (8-12c) to Kamakura period (12-14c). The prosperous Sugihara-gami gradually moved into decline in the 18 century. The cause was not for a decrease in demand of paper but for a transfer of the center of paper making site from an economically advanced place to a developing place. The conventional center of papermaking converted into other more efficient industries. The major cause would be the following: A variety of industry like afforestation business, charcoal making, and dried konjac (a jelly-like food made from the starch) production started in Sugihara valley, resulting in the increasing number of people who changed the job; The production of Kozo decreased thus more and more materials are purchased from other areas, resulting in the low profitability of paper industry. There were several farmhouses of making paper in Mitani, Shimizu, Hasegai, Kadomura in Sugihara valley in the beginning of Taisho period (early 20 c). However, young people engaged in other occupations increased year by year. Only old people somehow kept the tradition of Sugihara-gami which had been inherited from their remote ancestors. The long history of papermaking, which had continued since the 7th century in Sugihara valley finished in Taisho 14 (1925) owing to a gradual decrease in the farmhouses. The papermaking in the Sugihara Valley stopped due the overwhelming presence of western paper for several decades, but it achieved its revival; The trigger was a study of Japanese paper by Dr. Jugaku Bunshou, which brought the rare paper of "Sugihara-gami" to the public again. Dr. Jugaku visited Sugihara Valley Village with Dr. Shinmura Izuru in Showa 15 (1940), and proved that Sugihara-gami, a byword for Japanese paper had been made in this place. Mr. Fujita Sadao, who was a local history researcher in this town, was deeply impressed with it, and conducted an original study. During Showa 40's (1965-1974) when people began to pay attention to enriching and fullness of heart after Japan achieved the rapid economic growth, they started to take actions for the recovery of Sugihara-gami which had a bright history and a long tradition. A monument of Sugihara-gami’s birthplace was built in the school ground of Sugihara Valley Elementary School by volunteer staffs in Showa 41 (1966). Mr. Fujita published "Sugihara-gami" in Showa 45 (1970), which was the compilation of his study on Sugihara-gami for 30 years . Also, in the same year, tools for paper making were gathered with the lead of elderly people who had experience of paper making. Indeed, after an interval of 50 years, the revival of Sugihara-gami papermaking was finally achieved in the present day. |
◆Exhibition / Showcase
Sugiharagami Kenkyujo (Sugihara Paper Laboratory)
(We produce and sell a variety of products using Sugihara-gami)
768-46, Torima, Kami word, Taka town, Taka district, Hyogo prefecture
679-1322
TEL: +81-(0)795-36-0080 (Japanese only)
Assistance needed? For inquiries in English:
JTCO Contact Form
Your inquiries will be forwarded by JTCO in Japanese to the organization you wish to contact.