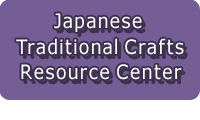
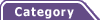
Total:131items
- Pottery & Porcelain (18)
- Lacquerware (4)
- Glasswork (2)
- Wood & Bamboo Work (19)
- Leather Work (1)
- Papermaking (13)
- Mino Washi: Mino Japanese Paper
- Ogawa Washi handmade paper
- Tegaki Koinobori (Hand-drawn Carp Streamer)
- Touzan-Washi: traditional Touzan Japanese Paper
- Sugihara-gami: Sugihara paper
- Najio-shi: Najio paper
- Nishinouchi Washi : Nishinouchi Japanese paper
- Yatsuo washi paper
- Yoshino Tesuki Washi: Yoshino Handmade Paper
- Gokayama Washi Paper
- Izumo Mingeishi: Izumo Folk Craft Paper
- Kurotani Washi: Kurotani Japanese paper
- Tosawashi:Handmade Japanese Paper
- Textile (20)
- Dyeing products (5)
- Masonry (1)
- Metal Work (11)
- Stationery (4)
- Livingware (3)
- Accessory (4)
- Toys & Entertainment (14)
- Interior (2)
- Other crafts (10)

![]() |
Main Production Site:Iwate |
Touzan-Washi, or traditional Touzan Japanese Paper, has been inherited since as long as 800 years ago in Tozan-town, Ichinoseki City, Iwate Prefecture.
Touzan-Washi is mainly produced in cold winter. Its features are delicate, soft and strong quality with natural color and warm feel of camellias. The paper is used in various ways: shoji (paper screens in traditional Japanese houses) paper, calligraphy paper, award certificates, colored paper, business cards, postcards, letter paper, and more. Also, these characteristics are used in their local specialities: strong and simple "Shifu-ori" made of strings of striped and looped washi and soft and winsome "Washi-men (mask)" of okame and hyottoko faces.
Today, however, there are only a few artisans mainly in Yamaya hamlet, who continue to produce simple and strong paper mostly from camellias while preserving the tradition and adherent to the distinct techniques.
[Iwate-Prefecture Traditional Craft]
Information provided by: Kamisuki Kan
Translation by Shione Furuta, reviewed by Tomoko Yamamoto
Materials | Camellias, glue, etc. |
---|---|
Crafting Processes | [1. Edging camellias]
Edge camellias in late March in Touzan though normally from late autumn to early winter in most of the other areas. [2. Steaming camellias] Trim the branches and steam them in a cauldron. [3. Barking] Pour water over the branches immediately after steaming (It makes the barks shrink and easy to be taken away). Then, bark them before they become cold. [4. Drying black barks and pulling white barks] Bundle the barks and dry them hung under eaves and such. Reconstitute the well-dried barks in water and scrape off the outer black barks with a knife between farming from April to early Autumn. Dry the inner white barks again and store them till the time of paper pressing. [5. Soaking and washing in water ] Soak the white barks in running water and wash them well. Wash off excrescences such as small pieces of black barks and sand before boiling. [6. Boiling] Put soda ash in a cauldron and boil. Then, put the white barks detangling them and boil them again for two hours. During the boiling, rotate them to heat them evenly. Soda ash helps remove impurities from the white barks. [7. Removing scum] Remove scum from the boiled barks in a bamboo basket soaked in running water. [8. Removing dirt] Check each bark and remove small pieces of black barks and discolored scars carefully to make paper without dirt. [9. Beating] Set the barks in a machine and beat them until each fiber separates. [10. Separation] Agitate the fibers by a Naginata (literally meaning a long-handled sword) beater. It separates the fibers completely by circulating them in the water and cuts them into the same length by the rotation of the blade. [11. Preparation for pressing paper] Put the ingredients into a Sukibune (a tool which looks like a boat), beat them well with a harrow. Then, pour glue and beat them well with a bamboo stick to blend the glue and the ingredients. The glue separates the fibers in the water and they get dispersed evenly. [12. Pressing paper] Dip the ingredients up with a Suketa (a wooden frame used to press paper) and sway them to make paper. The way to press depends on ingredients and production areas. In Touzan, washi artisans sway them vertically and horizontally and entangle the fibers. Place the finished paper on a drainboard out of the frame, pile each of them on a board called "Kamidoko". [13. Compression] Leave the paper overnight and let the water run. Place a board on the paper and drain off them compressing with a jack gradually. Compress them until each piece of them is wet. [14.Drying paper] Scale each piece of paper and apply it with a brush to a dryer made of a stainless plate. Dry it by heat of steam in the dryer. Though they dry paper in the sun in some temperate areas, people in this area of cold winter use steam because it is not affected by climate. When the paper dry completely, it's finished. |
History | This area is called "Touzan" because the landscape toward east from Mt. Tabashine near Chuson-ji Temple looks like Higashiyama in Kyoto. It has also become the name of the paper.
In late Heian period (8-12c), warriors of the Fujiwara clan, which was devastated by the Minamoto clan dominant in Kamakura, fled from Oshu-Hiraizumi and started living around Tozan town. They are said to have started producing paper as commodity while farming. This tradition has passed down for 800 years until now. According to literature, paper pressing became popular since 1831 when two artisans were recorded and was further encouraged by the Date Domain. There were reportedly more than 150 artisans in 1715. It is said that almost all hamlets in Nagasaka and Tagoutsu of the town pressed paper at the peak, from the end of Edo Period (17-19c) to Meiji Period (19-20c). In 1942, nearly 300 artisans pressed paper as s second job during winter and had a wide channel for sales around Tohoku region as well as in Iwate Prefecture. |
Related URL | http://www.echna.ne.jp/~nobuhiko/ |
◆Exhibition / Showcase
Kamisuki-kan (House of Paper Pressing)
Opening hours: 9:00-17:00 (April-November) / 10:00-15:00 (December-March)
Holidays: Open every day (April-November) / No scheduled holidays (December-March) ※ In-advance contact is prefereble.
Address: 390, Nagasaka-azamachi, Higashiyama-cho, Ichinoseki City, Iwate Pref. 023-0302
Tel: +81-(0)191-47-2424 (Japanese Only)
Fax: +81-(0)191-47-2436
◆Event Information
Paper pressing experience is available at "Kamisuki-kan".
Experience Tozan-Washi Papermaking (Japanese Only)
Assistance needed? For inquiries in English:
JTCO Contact Form
Your inquiries will be forwarded by JTCO in Japanese to the organization you wish to contact.