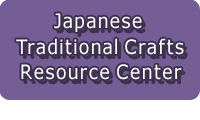
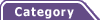
Total:131items
- Pottery & Porcelain (18)
- Koshu Kimen Gawara: Koshu Tile with a Devil’s Face
- Hasami Yaki: Hasami Porcelain
- Kiyomizu Yaki: Kyo style ceramics, Kiyomizu ware
- Otani Yaki: Otani Pottery
- Izushi Yaki: Izushi Porcelain
- Onta-yaki: Onta Pottery
- Takahama Yaki: Takahama Porcelain
- Mushiake- Yaki: Mushiake ware
- Kikuma-Gawara: Kikuma Roof-Tile
- Zeze-Yaki: Zeze ware
- TsutsumiYaki: Tsutsumi Pottery
- Hira Shimizu Yaki: Hira Shimizu Ware
- Tajima Banko Yaki: Tajima Banko Pottery
- Shidoro-Yaki: Shidoro Ware
- Amakusa Tojiki: Amakusa ware
- Shibukusa-yaki: Shibukusa ware
- Karatsu Yaki : Karatsu Ware
- Satsuma-yaki : Satsuma Ware
- Lacquerware (4)
- Glasswork (2)
- Wood & Bamboo Work (19)
- Leather Work (1)
- Papermaking (13)
- Textile (20)
- Dyeing products (5)
- Masonry (1)
- Metal Work (11)
- Stationery (4)
- Livingware (3)
- Accessory (4)
- Toys & Entertainment (14)
- Interior (2)
- Other crafts (10)

![]() |
Main Production Site:Okayama |

The greatest appeal of Mushiake-Yaki (Mushiake ware) is its quiet color that comes from ash glaze. Mushiake-Yaki goes well with any kind of pottery particularly at tea ceremonies.
Other specialties are as follows.
[Clay]
The clay used for Mushiake-Yaki is mainly mountain clay, which is viscous, firm and fire-resistant. It is mixed with other materials and elutriated to make its original clay according to the tradition.
[Glaze]
The transparent glaze which gives distinctive taste to Mushiake-Yaki is made from refined natural pine tree ash at each pottery. Potters are careful about choosing clay because quality of the clay is determinant of the color of the ware.
[Design]
Influenced by Kyoto style, thin-made Mushiake-Yaki is sensitive and refined, and old Kyoto ceramic style can be seen in its rustic shape.
[Tone of the Glaze]
The additional glaze makes gradation to the original colors of quiet blue, red and yellow made by ash glaze. The way of burning pinewood can also change the color tones.
Traditional Craft Officially Designated by the Prefecture
Source of information: Mushiake-Yaki Kamamoto (Mushiake-Yaki Potteries)
Translation: Marina Izumi, reviewed by Naoko Yamashita
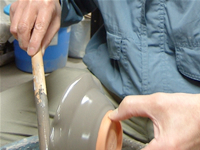
Materials | Clay, transparent ash glaze |
---|---|
Crafting Processes | 1.
After shaping the clay on a potter's wheel, and when the clay is dried to leather-hard state at which point it is easy to shave the clay, trim the bottom of the piece and make a foot. Then, natural dry the piece to evaporate water in the clay for the following step. 2. Biscuit fire the piece at 800℃ (at highest). After biscuit firing, the piece is ready for glazing. 3. Now the piece is forwarded to the next step. The glaze mainly used for Mushiake-Yaki is produced from natural pine tree ash. Ash and other materials are blended and mixed well with a dipper to make original glaze. Some types of materials cause precipitation at the bottom, therefore, this process requires close attention during the mixing process. 4. When the glaze is ready, the biscuit fired piece is immersed into the glaze. Colors and tones on the piece after firing are affected by thickness of the glaze. With thick glaze, color tones tend to get dark and more cracks called "Kan-nyu" can be made on the surface due to the different contraction between the clay and the glaze. With thin glaze, on the other hand, color tones tend to get light with less "Kan-nyu". And sometimes surface gets browned in accordance with the thickness of glaze, which gives good taste to the product. 5. Fire the glazed piece at a high temperature of 1250-1280℃. When the temperature in the kiln becomes 950℃, put split firewood of pine tree into the kiln from the fire port, which makes almost oxygen-free state. Inside the kiln, chemical reaction is caused by the pine tree smoke, which influences the color of the glaze ? with more influence, glaze color changes to light green, whilst with less influence by the smoke, the color changes to loquat color. Those colors are determined by the conditions inside the kiln ? the way of burning pinewood, position that pieces are put; sides of the pieces exposed to the smoke. |
History | There are various views about the origin of Mushiake-Yaki, which is still unknown. But it is said to have started 300 years ago.
Mushiake district was a feud of the Iki family. The patriarch of the family was the head of Chief Retainers in Okayama Province with 33,000 koku(approximately one thousand inhabitants). And Mushiake-Yaki was born as "Oniwayaki" which was a habit of feudal lords where they invited potters to their land and had them create potteries to their preference. At the time of Iki Tadasumi the 14th (also known as Sanensai), who was a great master of the tea ceremony, he invited skillful potters in Kyoto such as Seifu Yohei, Raku Chozo and Miyagawa Kouzan and supervised the style of Mushiake-Yaki. This is why the style was transformed to a delicate style with Kyoto flavor like "Awata-Yaki" . Master Iki Sanensai was exactly the restorer of "Mushiake-Yaki" and Mushiake-Yaki was created to be used for tea ceremonies. |
Related URL | http://www.musi.co.jp/ |
◆Exhibition / Showcase
・Mushiake-Yaki Kamamoto
4493, Okucho Mushiake, Setochi-shi, Okayama, 701-4501, Japan
TEL: 0869-25-0413
(Japanese only)
Opening Hours: 9:30~18:00 (irregular holidays)
Potters: Kuroi Sensa, Kuroi Keiun, Kuroi Hiroshi
・Central Public Hall, Ota's Collections in Exhibition Room of Mushiake-Yaki
465-1, Okucho Owari, Setouchi-shi, Okayama, 701-4221, Japan
TEL:0869-22-3761
FAX:0869-22-3762
(Japanese only)
Assistance needed? For inquiries in English:
JTCO Contact Form
Your inquiries will be forwarded by JTCO in Japanese to the organization you wish to contact.