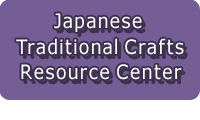
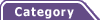
Total:131items
- Pottery & Porcelain (18)
- Lacquerware (4)
- Glasswork (2)
- Wood & Bamboo Work (19)
- Leather Work (1)
- Papermaking (13)
- Mino Washi: Mino Japanese Paper
- Ogawa Washi handmade paper
- Tegaki Koinobori (Hand-drawn Carp Streamer)
- Touzan-Washi: traditional Touzan Japanese Paper
- Sugihara-gami: Sugihara paper
- Najio-shi: Najio paper
- Nishinouchi Washi : Nishinouchi Japanese paper
- Yatsuo washi paper
- Yoshino Tesuki Washi: Yoshino Handmade Paper
- Gokayama Washi Paper
- Izumo Mingeishi: Izumo Folk Craft Paper
- Kurotani Washi: Kurotani Japanese paper
- Tosawashi:Handmade Japanese Paper
- Textile (20)
- Dyeing products (5)
- Masonry (1)
- Metal Work (11)
- Stationery (4)
- Livingware (3)
- Accessory (4)
- Toys & Entertainment (14)
- Interior (2)
- Other crafts (10)

![]() |
Main Production Site:Saitama |
Ogawa-machi, little Kyoto in former Musashi region (current Tokyo, Saitama and Kanagawa Pref.), where Chichibu mountains and people's life rooted in Kanto Plain have interacted, has flourished as a craftsmen's town which features manufacturing with advantage of blessings of nature products such as furnishings, silk, sake, and Washi, or Japanese handmade paper. Particularly, based on manufacturing techniques employing the traditional producing method used in manufacturing Hosokawa Washi paper, Ogawa Washi has developed sensitively and broadly responding to varied demands in Tokyo since the capital was formerly called Edo in the 17-19th century. The technique which has deepened and evolved along with everyday changing life and the tradition inherited from Hosokawa paper have been passed down by craftsmen for generations, which draw many people to Ogawa Washi.
[Saitama prefectural governor-designated traditional handicraft]
Information & materials provided by: Kubo Paper-making Company
Translation by: Tomoko Yamamoto
Materials | Kozo (Paper Mulberry), Mitsumata (Paper Bush), and Gampi (Diplomorpha sikokiana) |
---|---|
Crafting Processes | Washi paper making is well known for its producing processes referred to as "Kami-suki", or making paper from wet, pulpy material by spreading thin and drying it, and "Ita-boshi", or drying wet paper by spreading it on wooden boards in the sun. However, this actual Washi making site creates Washi through manifold processes: starting from procurement, processing, and preparation of materials through selecting and processing to finishing product.
[Processes of Washi paper making] 1: Materials The three kinds of plants, Kozo (Paper Mulberry), Mitsumata (Paper Bush), and Ganpi (Diplomorpha sikokiana), the representative materials for Washi making, produce different types of paper respectively due to their different features as plants. 2: Material processing Steaming Cut raw timbers into appropriate size for a large pot (about 70 cm long at this studio), , then bundle the timber pieces and steam them in a large pot for approximately 2 hours. After the steaming process, 3-4 buckets of water is poured onto the pot to facilitate stripping bark from the wood. Taken from the pot, the steamed timber pieces are covered with straw mats to keep them warm. Stripping bark Only the outermost bark are stripped from steamed Kozo and then sun-dried until they get dry completely. Scraping Kozo bark consists of three layers : "kuro-kawa" (black bark), "ama-kawa" (green bark), and "shiro-kawa" (white bark) from the outermost. Shiro-kawa, or innermost white bark, contains many fibers serving as material for Washi. Kozo-hiki, or Kozo peeling is scraping Kozo's outermost bark, the amount of which depends on the types of Washi to be produced. As the preliminary step, the sun-dried Kozo is soaked in water to make it soft. The Kozo with its outermost bark peeled are reserved until it is used. 3: Cooking and Cleaning Boiling increases softness of sun-dried material which is again softened by soaking in water beforehand. Extracting impurities, followed by rinsing off harshness and then removing dusts, leaves only top-quality fibers which serve as essential material for paper. Cooking Dry-reserved Kozo needs to be softened by soaking in water tank for a few days prior to boiling. A few hours of boiling in a solution with alkali chemical such as soda ash and caustic soda at the ratio of 15-20 % of the Kozo weight dissolves impurities out from the softened dried Kozo bark, which further softens the material. A traditional method would use wood and plant ashes. In Ogawa-machi, people call this boiling method "Kazu-ni", or Kazu-boiling because Kozo has been historically called "Kazu" in this area. Washing and removing foreign particles In Ogawa-machi, people call this process "Kattsuashi", a term corrupted from "Kazu-sarashi" meaning Kozo bleaching. The whole process from dust removing to "Chiri-tori", or dust removing, is locally referred to as "Kattsuashi", or Kozo bleaching, though a term "Sarasu" (bleaching) strictly means removing harshness and bleaching. The process which would formerly take place in the river is today done in water tanks. Instead of the conventional method of bleaching Kozo fibers by making use of action by the sun's ultraviolet rays and oxygen in water through soaking the material in flowing water for a few days, "Sarashi" generally applies chlorine bleaching today. Sometimes only harshness is removed from the material, which is called "Mi-sarashi", or unbleached. Another process follows bleaching: "Chiri-tori" or removing dust. Dust, not-softened fibers, and strings are removed from bleached Kozo which is pulled up with sticks little by little. Removed dusts called "Yogo" are utilized for another purpose with other by-products such as stripped barks. 4: Beating This work sleaves Kozo fibers by beating the material with bars made of hard woods such as oak so that fibers can be scattered in water in the next process of Kamisuki (paper making). Currently, machines undertake the following two works. Dakai (Stomper-beating) A machine beats Kozo by repetitively springing a weight called "Taiko" up and down for 30 minutes. Koukai (Machine-Beating) A gigantic mixer-like machine beats the material, weight-beaten Kozo in 5 minutes. The use of the final product decides on the duration of this machine-beating process, because the texture of western paper material (wooden pulp) depends on the time of this loosening process. Kozo fibers after beaten are well sleaved like cotton. 5: Kamisuki (Washi paper making by spreading pulpy materials thin to dry) The fluffy material produced as above and "Neri" (a mucilaginous agent) such as sunset hibiscus (Hibiscus manihot) are placed in a water tank and Washi is produced sheet by sheet. Tools Sukifune (Boat-shaped papermaking tank) … Tank containing water, materials and a mucilaginous agent Maguwa (Harrow) … A tool for stirring materials in the sukifune tank Sukiketa (Deckle) … Wooden frame for papermaking Sukisu (Bamboo screen) … Screen made of thin bamboo strips, used for papermaking Yumi (Suspension) … Tools made of bamboo for hanging deckles Shikizume (Stand) … A stand where produced wet paper is spread and piled (This term is used only in Ogawa-machi) "Neri" (a mucilaginous agent) "Neri", or a mucilaginous agent, for which Tororo-aoi, or sunset hibiscus (Hibiscus manihot)is typically used, locally called "Toro". Toro's mucilage is filtered into the tank and re-stirred. Instead of serving as glue, "Toro" has following two major functions: - Even dispersion of Kozo fibers in the tank creating even coverage of fibers on paper. - Slowing liquid filtering with Su (bamboo screen) which allows time to shake Keta (deckle) and make movements on surface. Kamisuki (Paper making-spreading thin to dry) Scoop the liquid with a deckle which has a screen in between, move the deckle, create desirable thickness of Washi by adding liquid, and dispose waste liquid ? this is a set of paper making work. The first scoop called Kesho-mizu produces a thin fiber layer on a bamboo screen. Followed by another scoop added, paper is strengthened by moving the whole deckle as if making waves in order to enable Kozo fibers to spread well entangled on the screen. Transparency on the screen tells paper's thickness. The liquid is removed from the screen when it reaches desired thickness, and Kamisuki (paper-making) work completes. Piling Washi sheets on "Shito" floor Finished yet still wet paper called "Shisshi" is piled up on "Shito" floor behind the workplace. 1-day paper-making work produces 10-some to even some-10 cm of paper layers in height, depending on its thickness. 6: Compressing Paper-making work is repeated 150-200 times a day, creating a huge pile of wet paper which is called "Kanda". Then Kanda is placed on a stand and compressed with equipment such as a hydraulic jack for dehydration. This work is done slowly over time because a strong quick push extends paper excessively. 7: Drying Sheets of compressed wet paper are taken off sheet by sheet and placed on iron or wooden boards. Carefully placing a sheet on a board from center outward prevents wrinkles from being made. There are different methods of drying, such as "Teppan-kanso (Iron board drying/Vapor drying)" and "Tempi-boshi (Sun-drying/Board drying)". Teppan-kanso (Iron board drying/Vapor drying) This method dries paper with heat generated by filling stainless-steel-made panels with hot water. The process completes in 2-5 minutes, depending on thickness of paper to be produced, regardless of weather. The finished paper displays flat and smooth surface with more hardness than the sun-dried one. Tempi-boshi (Sun-drying/Board drying) The board drying method dries wet paper by stretching it on wooden boards in the sun. Generally, 1-3 hours of sun-drying completes both sides of paper, depending on seasons and time of the day though. 8: Selecting and processing Dried paper is sorted out sheet by sheet, selecting accredited products from non-accredited which has defects, spots and irregular thickness.Some paper is finished as end products through varied processing based on its intended use. |
History | Origin: Implications from historical documents
Given that no documents which clearly tell the origin of Ogawa Washi have been found to date, there is nothing for it but to presume from the existing books. Among them, firstly, the most historical description showing that Washi was produced in former Musashi Province including Ogawa-machi was found in the Shoso-in Treasure House in the Nara period (774), saying "480 units of paper and 50 brushes paid as tribute by Musashi Province". Secondly, a few centuries later in the Heian period (927) also sees paper paid by former Musashi Province as young men's tribute. These records signify that paper was produced 1200 years ago in former Musashi Province. It is pointed out, however, that these descriptions cannot be directly linked to the origin of Ogawa Washi due to their unclear definition about areas where Washi was produced in the Province. In the meanwhile, based on "Ruiju-sandaikyaku", a code written in 841, depicting paper making in Obusuma-gun (the present Yorii-cho) adjacent to Ogawa-machi, it is conjectured that paper was also manufactured around Ogawa-machi in the same period (mid-9th century). Origin: Implications from ancient events in the surrounding areas Another presumption is held based on ancient events in the areas surrounding present Ogawa-machi. There was very often-said story that about a century before the Shoso-in Treasure House description, transcribing sutra often took place associated with foundation of Jiko-ji Temple in present Tokigawa-cho neighboring Ogawa-machi (673), which may be related to the origin of Ogawa Washi. However, a negative opinion appears today, making it difficult to refer to the above story as the origin. A finding that Korai-gun was founded with people from Goguryeo (kingdom of Korea) dwelling together in 716 brings a new view that paper making may have been introduced from them as a new technique. Origin: General view on the origin At present, the origin of Ogawa Washi is generally said to date back about 1300 years for the following reasons: (1) The record of paper-making in Obusuma-gun described in Ruiju-sandaikyaku code implies that paper was certainly produced in Ogawa-machi as well 1150 years ago. (2) Geological suitability for Washi paper making and the necessity to pay taxes by goods other than farm products offer conjecture that the Shoso-in Treasure House's paper-making description in former Musashi Province about 1200 years ago may include Ogawa-machi. (3) There should have been a maturation period of paper-making techniques until it met the quality to be offered as tributes. For the above reasons, it is often considered that the origin of Ogawa Washi dates back 1300 years, taking a century of the maturation period into account until it was recorded in the Shoso-in Treasure House archive. |
◆Exhibition / Showcase
Kubo Paper-making Company
1116-2 Ogawa, Ooaza, Ogawa-machi, Hiki-gun, Saitama Pref. 335-0321
Tel/Fax: 0493-72-0436
Open: 8:00 - 8:00 (Closed on Mondays)