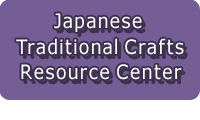
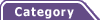
Total:131items
- Pottery & Porcelain (18)
- Lacquerware (4)
- Glasswork (2)
- Wood & Bamboo Work (19)
- Leather Work (1)
- Papermaking (13)
- Mino Washi: Mino Japanese Paper
- Ogawa Washi handmade paper
- Tegaki Koinobori (Hand-drawn Carp Streamer)
- Touzan-Washi: traditional Touzan Japanese Paper
- Sugihara-gami: Sugihara paper
- Najio-shi: Najio paper
- Nishinouchi Washi : Nishinouchi Japanese paper
- Yatsuo washi paper
- Yoshino Tesuki Washi: Yoshino Handmade Paper
- Gokayama Washi Paper
- Izumo Mingeishi: Izumo Folk Craft Paper
- Kurotani Washi: Kurotani Japanese paper
- Tosawashi:Handmade Japanese Paper
- Textile (20)
- Dyeing products (5)
- Masonry (1)
- Metal Work (11)
- Stationery (4)
- Livingware (3)
- Accessory (4)
- Toys & Entertainment (14)
- Interior (2)
- Other crafts (10)

![]() |
Main Production Site:Gifu |
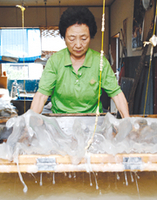
Washi (The Japanese Paper) such as Mino-Washi, can be used before any processing generally. Mino-Washi can be applied for different purposes and fields to produce different kinds of paper-made products including envelopes, postcards, letter paper, and business cards. Mino-Washi can be also used for restoration of cultural documents and for backing of hanging scrolls or rolled draperies. For making paper sliding doors and paper lanterns, Mino-Washi is suitable as well.
[A country designated traditional craft (Designated by the Minister of Economy, Trade and Industry)]
Photos & articles: Mino-Washi Brand Cooperative Association
Translation: Naotake Kakehi, reviewed by Chan Yitin
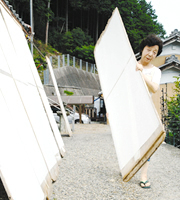
Materials | Kozo (Paper Mulberry), Mitsumata (Paper Bush), Gampi (a clove-like bush) |
---|---|
Crafting Processes | 1. Reaping
Washi is made from “Kozo,” paper mulberry, which is a species of deciduous low trees in the Mulberry family. On or about the winter solstice, Kozo shrubs are reaped while the root would be left for regrow, so that it is able to harvest the same shrub again in the next year. 2. Steaming Reaped Kozo are steamed in a large pot covered with a lid. 3. Ripping the bark The bark of steamed Kozo is ripped while it is still warm. Then a pile of bark is hung out on the bamboo pole to dry once. 4. Peeling Dried Kozo bark is soaked in water to make it soft. Then its surface black layers (outer bark) are scraped by a knife like tool named "Taguri-Kama”. As a result, only the white part (inner bark), which is what paper is made from, is obtained. The inner layer of the bark is exposed to sunlight and dried again. 5. Soaking in water The dried inner bark is placed in a shallow part of a river or in a tank of water for two or three days in order to wash out impurities and be bleached. 6. Boiling Softened inner bark is boiled in a large pot with "Aku," sodium lye, which melts and breaks down the glue like fibers in the bark. 7. Dusts removing After boiling, the inner bark has turned soft and become fiber-like paper material. The paper material is taken out from the pot and sent to washing area for washing. In washing area, the paper material is put in colander and impurities are washed out by flowing water. After that, the small dust is picked up carefully by hands. 8. Koukai (Hitting) The cleaned paper material is hit by the wooden hammer to make the fibers finer and thinner. 9.Kamisuki (Paper Milling) The paper material is mixed with water in “Shikifune” (a large tray) and stirred by a harrow. Then, a proper amount of liquid extracted from roots of “Tororoaoi,” is injected to adjust the viscosity of whole mixture. “Sukiwaku” ( a screen tray made of bamboo), is dipped into the mixture and scooped up. By moving the tray back and forth, tilting it from side to side, a moderate thickness film of paper is formed on the tray. 10.Dehydration Sheets of wet paper, which is called "Shito," are overlaid on a wooden board, which is called "Shikizume." For dehydration, Shito on the Shikizume is set on a compressor and sandwiched with another board. Then, by the pressure of heavy stones or jacking up, water in Shito is squeezed out. After this step, water in the paper is reduced to 60-65%. 11. Desiccation The Washi is taken off from dehydrated Shito one by one, and then attached on a drying board with its surface side up. While laying sheets on the board, the surface of each sheet is brushed gently with a brush made of horse mane to avoid any scratches or winkles on the sheet. The drying boards full of sheets of paper are brought outside and exposed to sunlight. 12.Inspection Sheets of sun-dried paper are stripped from its boards and collected. The condition of each sheet of paper is visually inspected carefully by holding against the light. 13. Products |
History | It is uncertain how Mino-Washi began, yet there is an old evidence found at the Shosoin Repository in Nara prefecture. The Shosoin Repository, which contains huge amount of documents from the Nara period preserves the national oldest "Family Register," and the paper of those registers is either Mino-Washi, Chikuho-Washi, or Chikuzen-Washi. Therefore, you can assume that Mino-Washi did exist since at least A.D. 702. Mino-Washi is known to be the highest quality among those three brands.
In the age of Heian period, there was a sharp rise in demand for Mino-Washi. Such demands could be attributed to the development and widespread of Buddhism, which lead to requirement of more copies of Buddhist scriptures. As the paper became popular, various kinds of paper were gathered in Kyoto and Nara. Even though there were many different kinds of paper, Mino-Washi received the accolade of being good quality among the people in the cities. Well-heeled people in Kyoto pulled the strings and tried to obtain the rarely offered Mino-Washi. Mino-Washi saw its highest consumption in Kyoto during Ounin and Bunmei era (1486-). It is considered that Mino-Washi industry grew rapidly during those ages synchronizing the evolution in trading and manufacturing of the ages. |
Related URL | http://www.minowashi-japan.com/access |
◆Exhibition / Showcase
Mino-Washi Museum (Japanese)
1851-3 Warabi, Mino City, Gifu Prefecture,
501-3788, Japan
Tel: 81-575-34-8111
Fax: 81-575-34-8280