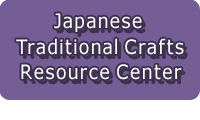
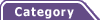
Total:131items
- Pottery & Porcelain (18)
- Lacquerware (4)
- Glasswork (2)
- Wood & Bamboo Work (19)
- Leather Work (1)
- Papermaking (13)
- Textile (20)
- Dyeing products (5)
- Masonry (1)
- Metal Work (11)
- Stationery (4)
- Livingware (3)
- Accessory (4)
- Toys & Entertainment (14)
- Interior (2)
- Other crafts (10)

![]() |
Main Production Site:Hiroshima |
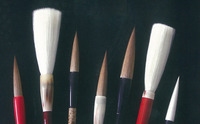
The main material for Kawajiri brush is animal hair. High quality technique “neri-maze (kneading mixing)” was firstly used, and then “bon-maze” technique was also adopted, which made mass production possible. Through this innovation, Kawajiri brush gradually became known across Japan. In order to make a brush, sincere efforts made by many craftsmen and various processes are necessary.
Kawajiri brush is hand made one by one using a traditional process. Craftsmen make the most of their skill and put their enthusiasm and affection through all the process of making one brush.
[Nationally designated traditional craft (by minister of Economy, Trade and Industry)]
Provided by Kawajiri Brush Cooperative Association
Translation by: Haruka Kumada, reviewed by Tham Wan Xin
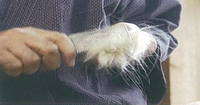
◆Exhibition / Showcase
For more Infomation
Kawajiri Brush Cooperative Association
1-2-2 Kawajirinishi, Kure-shi, Hiroshima 737-2603 JAPAN
TEL: +81-(0)823-87-2395
(Japanese only)
Kawajiri Brush Museum
502-39 Kawajiri-cho, Kure-shi, Hiroshima 737-2631 JAPAN
TEL: +81-(0)823-87-2390
(Japanese only)