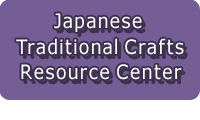
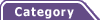
Total:131items
- Pottery & Porcelain (18)
- Koshu Kimen Gawara: Koshu Tile with a Devil’s Face
- Hasami Yaki: Hasami Porcelain
- Kiyomizu Yaki: Kyo style ceramics, Kiyomizu ware
- Otani Yaki: Otani Pottery
- Izushi Yaki: Izushi Porcelain
- Onta-yaki: Onta Pottery
- Takahama Yaki: Takahama Porcelain
- Mushiake- Yaki: Mushiake ware
- Kikuma-Gawara: Kikuma Roof-Tile
- Zeze-Yaki: Zeze ware
- TsutsumiYaki: Tsutsumi Pottery
- Hira Shimizu Yaki: Hira Shimizu Ware
- Tajima Banko Yaki: Tajima Banko Pottery
- Shidoro-Yaki: Shidoro Ware
- Amakusa Tojiki: Amakusa ware
- Shibukusa-yaki: Shibukusa ware
- Karatsu Yaki : Karatsu Ware
- Satsuma-yaki : Satsuma Ware
- Lacquerware (4)
- Glasswork (2)
- Wood & Bamboo Work (19)
- Leather Work (1)
- Papermaking (13)
- Textile (20)
- Dyeing products (5)
- Masonry (1)
- Metal Work (11)
- Stationery (4)
- Livingware (3)
- Accessory (4)
- Toys & Entertainment (14)
- Interior (2)
- Other crafts (10)

![]() |
Main Production Site:Gifu |
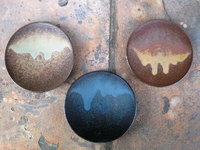
Koito-yaki (Koito pottery) uses two types of clays as its “clay body”, a mixture of clays to form a specific pottery. It uses mainly the local clay dug from a mountain in Hida Furukawa, a town about 20km north of Takayama City (Gifu Prefecture, central Japan), and additionally Gairome clay (a type of kaolin) from Seto City (Aichi Prefecture, bordered by Gifu) to increase refractoriness of the clay body.
Koito pottery is basically glazed with “Irabo glaze”, which is a traditional, brown glaze and known for its somewhat coarse texture.
Recently, by adding some pigments into Irabo glaze, “Ao-Irabo glaze” (‘ao’ means ‘blue’ ) has been newly developed and become the most popular glaze color among Koito pottery.
Ao-Irabo glaze produces a tasteful, deep cobalt blue color—a special color which can be seen only in Koito pottery.
Today, Irabo glaze has three colors: blue, brown and Uguisu (close to olive-green). These colors are created by varying mixing ratio of pigments contained in the glaze.
After firing, the pottery is so hardened and the applied glaze is well vitrified (becomes glass-like); thus, the pottery doesn't easily absorb smells of food and is welcomed as daily tableware. At first, it can be felt slightly coarse because of Irabo glaze, but characteristically, the more it is used, the smoother it becomes; and also, the color will get more and more tasteful.
[Local Handicrafts in Gifu Prefecture]
Courtesy of Koito Pottery
Translation: Tae Yamaguchi
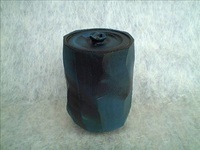
Materials | local clay from a mountain, Gairome clay and Irabo glaze |
---|---|
Crafting Processes | [1] Preparing for the Clay Body
Add water to the clay body, then wedge it well. [2] Shaping Wheel throwing: using “rokuro” (the pottery’s wheel), throw clay on the wheel and create an ideal shape. [3] Drying After shaping, the clay (greenware) still contains a large amount of water; the water turns into steam during firing, and it will cause cracking. Therefore, it is essential for the greenware to be dried enough before bisque firing. [4] Bisque Firing (First Firing) The dried greenware is so fragile that the first firing is needed to make it durable enough. [5]Glazing, and Glaze Firing (Second Firing) Apply glaze to the pottery (bisqueware), load it into kiln, and then start the second firing to achieve a “perfect” pottery; the glaze will be completely vitrified through this firing. [6]Cooling, and Unloading After the second firing, it is crucial for the pottery to be cooled slowly enough in the kiln, instead of rapid cooling; otherwise, the pottery will be exposed to sudden temperature changes and led to cracking or warping. Leave the pottery in, allow cool air to enter the kiln (whose temperature dropping should be controlled carefully), and finally, unload the pottery. |
History | During the Kan'ei era (1624-1644), KANAMORI Shigeyori, the lord of Hida Domain, invited a potter from Kyoto (central Japan) and allowed him to produce pottery at Koitozaka, the west of Takayama City—this is the origin of Koito pottery. The invitation was supported by his brother KANAMORI Sowa, who was the founder of Sowa-ryu school of tea ceremony and lived in Kyoto. However, it was not long before the pottery came to an end; it might be because the climate was too cold and not suitable for making pottery.
About 200 years later, in 1836, HOSOE Kasuke and HIRATA Chuemon, the local wealthy merchants, invested in restarting pottery-making; they invited a potter TODA Ryuzo from Seto and built their kiln at Koitozaka. However, it could not last more than 5 years after all. In the postwar period, NAGAKURA Saburo finally re-established a kiln and revived Koito pottery at the very same place. Since then, all products have been made entirely by hand—from wheel throwing to slab building, without relying on an electric wheel or casting molds. These skills are still being handed down through generations. |
Related URL | http://www.koitoyaki.com/ |
◆Exhibition / Showcase
Koito Pottery -“Traditional and Modern” TAKAYAMA Pottery
Address:
1-136, Kamiokamoto-machi,
Takayama-shi, Gifu, 506-0055
JAPAN
Tel : +81-577-32-1981
Fax: +81-577-33-8361
-Visitors are welcome to observe the studio (Pottery Trial is not provided).
◆Event Information
Hida Takayama Crafts Experience Center
- You can try a hands-on activity, “Painting on a HIDA Pottery”
- Located near Koito Pottery
For more details
Assistance needed? For inquiries in English:
JTCO Contact Form
Your inquiries will be forwarded by JTCO in Japanese to the organization you wish to contact.
*Please write the name of craft you wish to ask about.