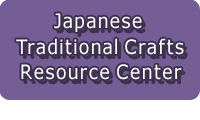
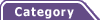
Total:131items
- Pottery & Porcelain (18)
- Lacquerware (4)
- Glasswork (2)
- Wood & Bamboo Work (19)
- Hakone Yosegi Zaiku: Hakone Marquetry
- Boshu Uchiwa: Boshu Fans
- Nikko-bori: Nikko carving
- Sasebo Koma (Sasebo Spinning Top)
- Shimoda Yanimatsu Zaiku (Shimoda Joinery of Oily Pine)
- Echizen Takeningyo (Bamboo Dolls)
- Osaka Senshu Kiri-dansu: Paulownia chest of drawers or wardrobes of Senshu, Osaka
- Kitayama Maruta: Japanese cedar logs
- Yodoegasa: Yodoe umbrella
- Atami Kusu Zaiku: Atami Camphor wood crafts
- Kawatsura Kokeshi Doll
- Itaya Zaiku: Itaya Bark Craft
- Yokohama Classic Furniture
- Hinaga Uchiwa: Hinaga Fan
- Torafu Takezaiku: Tiger Bamboo Work
- Tsuruzaiku: Woven Vine Craft
- Okawa Kumiko: Okawa Kumiko Wood Joinery
- Shuro Houki: Hemp-palm Broom
- Furyumen: Wood Carving Mask
- Leather Work (1)
- Papermaking (13)
- Textile (20)
- Dyeing products (5)
- Masonry (1)
- Metal Work (11)
- Stationery (4)
- Livingware (3)
- Accessory (4)
- Toys & Entertainment (14)
- Interior (2)
- Other crafts (10)

![]() |
Main Production Site:Fukuoka |
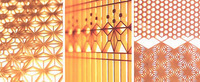
Okawa prides itself as Japan's greatest producer of tategu -- space dividing and partitioning furniture that is best represented by Japanese sliding doors fusuma and shoji. About 460 years ago, Okawa woodworkers started woodworking in the field of ship carpentry. Through division of labour in the woodwork industry into more specialized fields such as general carpentry and furniture making, the tategu industry also came to be developed.
With the passing down of traditional woodworking techniques from generation to generation, Okawa now produces a wide variety of partition furniture --- not only shoji (sliding doors or windows made with paper over a wooden frame), but also fusuma (sliding screens made with paper or fabric over a wooden frame), doors, amado (rain shutters), closet doors and the like, all of which fit in well with modern interior design.
Kumiko is a technique of making partition furniture by assembling pieces of wood without using nails. Grooves, holes and projections are added to thinly shaven strips of wood, which are assembled piece by piece whilst adjustments are made using tools such as planes, saws and chisels.
Craftwork created using the kumiko technique is known as Okawa Kumiko. It is said that Okawa Kumiko arose naturally as an ornamental accessory to partition furniture, amidst competition among partition furniture craftsmen to emerge as the most skilled in the trade. The designs of Okawa Kumiko take the form of more than 200 patterns, including Asa-no-ha (literally, hemp leaf; a traditional Japanese pattern that resembles the hemp leaf), Gomagara (literally, sesame pattern; a traditional Japanese pattern that resembles the sesame flower) and Yae-zakura (multi-layered cherry blossoms). Even today, craftsmen are making use of these patterns to create new designs of Okawa Kumiko.
[Governor-designated Traditional Handicraft of Fukuoka Prefecture]
Credits: Society for the Promotion of Okawa Traditional Craft
Translation by: Mavis Chng
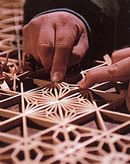
Materials | Wood |
---|---|
Crafting Processes | [1] Preparation of Wood
Wood used to make Okawa Kumiko must be dried for at least 5 years. Such wood is trimmed to 2 mm and sometimes below 1 mm, where thinner pieces are required. [2] Selection of Wood Okawa Kumiko is primarily made from Japanese cypress, but craftsmen also use Japanese cedar, hiba cypress, magnolia, lignitised Japanese cedar and lignitised elm. As there are subtle colour differences even among the same wood material, wood used to make Okawa Kumiko is also carefully selected based on its colour. [3] Kudegiri and Jigumi Selected wood material goes through kudegiri, which involves using a saw to make an incision to a precision of 0.001mm both vertically and horizontally, without breaking the piece of wood. This is followed by warikomi, whereby the incision earlier created is further refined with a special plane for narrow grooves. Warikomi ultimately depends on the craftsman's keen artistic sense that is trained over many years of being in the trade. The wood framework of jigumi put together by mitsukude, which is a method of assembling 3 pieces of wood that have been prepped by the processes of kudegiri and warikomi, forms the basic structure of kumiko. [4] Planning the Arrangement of Wood Parts Within Jigumi More than 200 traditional patterns of wood assembly are arranged within the jigumi framework, which is in turn housed in tsukeko. Tsukeko is a thin wooden frame set between the jigumi framework and the outermost frame. It serves as a supplementary frame to strengthen the structure and provides a surface for attaching the paper screen afterwards. The distribution of wood assembly patterns within the jigumi is done while ensuring aesthetic balance in the arrangement of wood parts. [5] Cutting and Trimming of Wood Material to Make Kumiki The wood components to be fitted within kumiko are known as kumiki. Kumiki is made using planes, saws and kehiki, which is a Japanese woodworking tool for making straight line markings on wood with a blade. As kumiko making is a craft where precision is of utmost importance such that even deviation by the thickness of a piece of paper can affect results, kumiko craftsmen make kumiki by trimming wood using their well-honed artistic sense and woodworking tools. The quality of tools used in kumiko making has a profound impact on the creation. [6] Assembly of Kumiki Numerous small kumiki parts are assembled while checking how tightly each kumiki holds together. Each kumiki is assembled to ensure that it fits snugly within the jigumi. [7] Variations of Kumiki With more than 200 traditional ways of assembling kumiki, this is a process that requires a keen eye for detail. Each craftsman's artistic sense is continually challenged and further perfected in this industry that demands accuracy to the micron level. [8] Assembly of Kumiki to form Kumiko Kumiko is made by assembling the finer and more detailed parts first. Sometimes, tens of thousands of kumiki components have to be fitted together in the process. While kumiko may look delicate, with not even the tiniest of a gap, it is as sturdy as a plank of wood. [9] Finishing Touches To round off the process, kumiko is fitted into partition furniture. While planing is involved when creating kumiko so that it does not collect dust easily, kumiko is sometimes further installed between glass panes to better maintain its delicate beauty. |
History | Kumiko decorate the balustrades of the Golden Hall of the Horyu-ji Temple (Horyu-ji Kondo), which is one of the oldest surviving wooden buildings and also regarded as the most representative building of the Asuka period (around 7c). Such kumiko make up the parts of the "卍" character. Accordingly, it is said that kumiko was introduced into Japan from China during this period as part of the architecture of shrines and temples.
Saws used to cut vertically first appeared in the 15th century and jointer planes (dai ganna) were introduced into Japan around the 17th century. It is believed that such tools morphed into woodworking tools similar to those that are used today during the 18th century. It follows that the intricate kumiko we see today developed around the same time. Okawa Kumiko boasts a history of 300 years, and its more than 200 traditional assembly patterns are being passed down to the next generation as part of an art that will become even finer than before. |
Related URL | http://okawa-dentou.jp/dentou/kumiko/ |
◆Exhibition / Showcase
Society for the Promotion of Okawa Traditional Craft
(Japanese only)
Centre for the Promotion of Okawa Interior Design (next to Okawa Industrial Association (Okawa Sangyou Kaikan))
Gobaru 483-8, Okawa City, Fukuoka Prefecture, 831-0028
Telephone: +81-0944-87-0035 (Japanese only)
Operating Hours: 8:30-17:00
Closed on: Saturdays, Sundays and Public Holidays
Assistance needed? For inquiries in English:
JTCO Contact Form
Your inquiries will be forwarded by JTCO in Japanese to the organization you wish to contact.
*Please write the name of craft you wish to ask about.