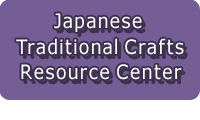
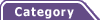
Total:131items
- Pottery & Porcelain (18)
- Lacquerware (4)
- Glasswork (2)
- Wood & Bamboo Work (19)
- Leather Work (1)
- Papermaking (13)
- Textile (20)
- Touzan-Ori: Touzan Weaving
- Sakai Gogatsu Koinobori: Sakai May Carp Streamer
- Nanbu Sakiori
- Nihon Shishu: Japanese Embroidery
- Tsuzurenishiki-Ori: Tsuzurenishiki Weaving
- Ojiya-Tsumugi: Ojiya Pongee
- Ise-Momen: Ise Cotton
- Ojiya-chijimi: Ojiya Crepe
- Yanai-jima: Yanai Stripes
- Kogin-zashi: Kogin embroidery
- Tamba Momen: Tamba Cotton
- Awa Shijira-ori: Awa Shijira Weaving
- Saga Nishiki: Saga Brocade
- Shinshu-Tsumugi: Shinshu-Pongee
- Kyo-nui: Kyoto Embroidery
- Noto Jofu: Noto-jofu hemp fabric
- Matsusaka Momen: Matsusaka Cotton
- Murayama Oshima Tsumugi
- Nibutani-attus
- Oku-Aizu Showa Karamushi Ori: Oku-Aizu Showa Ramie Textiles
- Dyeing products (5)
- Masonry (1)
- Metal Work (11)
- Stationery (4)
- Livingware (3)
- Accessory (4)
- Toys & Entertainment (14)
- Interior (2)
- Other crafts (10)

![]() |
Main Production Site:Niigata |
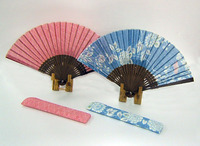
Ojiya-chijimi is made by weaving each warp thread and weft thread carefully, and the finished fabric has a flexible, nice, and soft feel.
It is not uncommon to spend two winters in order to make Ojiya-chijimi, designated as an Important Intangible Cultural Property, because of the time-consuming work from making yarn to completion of the cloth. The number of craftspeople making Ojiya-chijimi, which is difficult to produce in large quantities, are decreasing year after year, and the fabric was nationally designated as an Important Intangible Cultural Property by the Ministry of Education in 1955 to protect the production techniques.
[A traditional craft designated by the Minister of Economy, Trade and Industry]
Source: Ojiya Orimono Dogyo Kyodo Kumiai (textile industry cooperative association)
Translation: Tomoe Ukida, reviewed by Hiroko Okamura
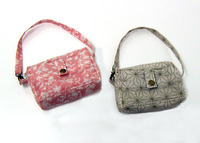
Materials | The material is hemp thread made from ramie, known as kimono fabric worn in midsummer. |
---|---|
Crafting Processes | Making yarn:
Twist the hemp weft tightly to create characteristic wrinkles of Ojiya-Chijimi. [Materials of yarn] Among hemp plants, perennial plant called choma (ramie) is used as yarn. [Twisting yarn] In order to create characteristic wrinkles of Ojiya-chijimi named shibo, twist the hemp weft tightly. Making kasuri (splashed pattern): Dye thread to produce kasuri. Based on the selected pictorial pattern, a ruler is made. Mark the weft with India ink while placing it along the edge of the ruler, and dye it by the surikomi (stenciling) method to make a pattern. [Rulers] Rulers for making kasuri appeared in 1680s. They are made by planning the width of fabric and the number of patterns based on the design. To make weft rulers, pile up several dozens to hundreds of shingles or cardboard sheets required for the design, cut the surface of the piled sheets to be flat, and copy the design on them. When they are used, each shingle or cardboard sheet is placed along the thread as a measure of dyeing. [Making kasuri (splashed pattern)] Stretch the weft thread tightly, place each weft ruler along the thread, and make ink marks on the parts of the thread where colors change, while adjusting the thread to marks showing both ends of the fabric. After the ink marking, tightly coil other threads around the parts which should remain white, and immerse the thread in a dye. This is called kasuri kubiri (tying). Although all kasuri patterns were traditionally made in this kubiri- gasuri method, the surikomi (stenciling) method was later adopted as fabric patterns became multicolored and complicated. Instead of immersing in dyeing liquid, the thread is dyed by applying multicolor dyes at a time in the stenciling method. After this method has been established, craftspeople started to create fine kasuri patterns at will. Weaving: Weave carefully by passing a colored weft thread through arranged warp threads, adjusting the pattern. [Weaving] It was after 1670 when various patterns such as stripes and kasuri patterns began to be made. Ojiya-chijimi, a traditional craft, is mainly characterized by the weaving pattern with full use of colored weft. The weaving requires patience as the width of the fabric and the selvages marked in kasuri making have to match to form the pattern each time a weft thread runs through warp threads arranged on a loom. Although the power loom has recently been introduced in place of the floor loom, this weaving method, adjusting the selvages and kasuri pattern every time a weft thread runs through warp threads, has not changed since the Edo Period (17-19c). Finishing: Fill a wooden vessel with tepid water and crumple the cloth with hands in the vessel to create wrinkles. After that, bleach it on the snow so as to make a distinctive texture and gloss. [Crumpling in tepid water] Fill a wooden vessel with tepid water and crumple a full role of cloth thoroughly with hands. In the process of creating wrinkles, the smooth fabric shrinks and vertical fine creases appear. This process has hardly changed since the Edo Period (17-19c). [Bleaching on the snow] Rinse the white crepe and place it on the snow. Then, the fabric turns white as snow. After bleaching, fix the wrinkles and dry the fabric. This bleaching is seen from the end of February to March when the sunlight is strong. However, the chances to see this scene are decreasing due to the development of processing technology and changes in the natural environment. |
History | It is said that weaving started in this region over a thousand and several hundred years ago. Blessed with various locational and natural conditions, it has developed since then.
The region was abundant with wild ramie of good quality, a textile material at the time, and people also grew the plants in the fields. In the Muromachi Period (14-16c), the Uonuma region developed into a major production area across the country. The skin of ramie is made into thread in the process called oumi, and the fabric woven with the thread is named Echogo-fu. It was first made as clothing for farmers' personal use in this snowy region and then gradually began to be used in business. Although the fabric was called jofu (high-quality hemp cloth) and plainly woven at the time, in the beginning of the Edo Period (17-19c), for the first time the weft was tightly twisted and woven into a comfortable crepe as kimono fabric for summer, with the finishing process to create wrinkles called shibo-tori, which is unique to Ojiya-chijimi. Producing the wrinkles on the fabric achieved an epoch-making success compared with a conventional hemp cloth, and the fabric was called Ojiya-chijimi. In less than ten years after its completion, it widely spread over the Uonuma region, laying the foundation of the present producing region of textiles including Ojiya City, Tokamachi City, and Minami-Uonuma City (Shiozawa and Muikamachi areas). |
Related URL | http://www.ojiya.or.jp/cloth/tijimi/ |
◆Exhibition / Showcase
Ojiya-shi Sougo Sangyo Kaikan Sun Plaza (industrial hall)
1-8-25, Jonai, Ojiya City, Niigata Pref. 947-0028
Tel 0258-83-4800
(Japanese only)
No admission fee
Opening hours: 9:00 am - 6:00 pm (until 5:00 pm in winter)
Closed: September 29 - January 3 (Orimono Kobo Orinoza and Shop Takuminoza are closed on Wednesdays)
Assistance needed? For inquiries in English:
JTCO Contact Form
Your inquiries will be forwarded by JTCO in Japanese to the organization you wish to contact.