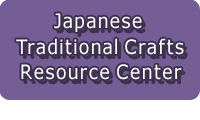
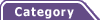
Total:131items
- Pottery & Porcelain (18)
- Lacquerware (4)
- Glasswork (2)
- Wood & Bamboo Work (19)
- Leather Work (1)
- Papermaking (13)
- Textile (20)
- Touzan-Ori: Touzan Weaving
- Sakai Gogatsu Koinobori: Sakai May Carp Streamer
- Nanbu Sakiori
- Nihon Shishu: Japanese Embroidery
- Tsuzurenishiki-Ori: Tsuzurenishiki Weaving
- Ojiya-Tsumugi: Ojiya Pongee
- Ise-Momen: Ise Cotton
- Ojiya-chijimi: Ojiya Crepe
- Yanai-jima: Yanai Stripes
- Kogin-zashi: Kogin embroidery
- Tamba Momen: Tamba Cotton
- Awa Shijira-ori: Awa Shijira Weaving
- Saga Nishiki: Saga Brocade
- Shinshu-Tsumugi: Shinshu-Pongee
- Kyo-nui: Kyoto Embroidery
- Noto Jofu: Noto-jofu hemp fabric
- Matsusaka Momen: Matsusaka Cotton
- Murayama Oshima Tsumugi
- Nibutani-attus
- Oku-Aizu Showa Karamushi Ori: Oku-Aizu Showa Ramie Textiles
- Dyeing products (5)
- Masonry (1)
- Metal Work (11)
- Stationery (4)
- Livingware (3)
- Accessory (4)
- Toys & Entertainment (14)
- Interior (2)
- Other crafts (10)

![]() |
Main Production Site:Niigata |
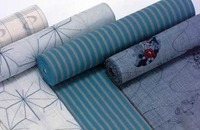
Ojiya Pongee is yarn-dyed fabric which succeeded the traditional technique of Chijimifu (a kind of hemp cloth). Among the Pongee, Yokosougasuri is representative for its full of elegance created by weaving with the tie dye yarn Kasuri-ito over the weft Yoko-ito. Ojiya Pongee is rated very highly for blending of its traditional skills creating unique texture of floss hand-spun yarn Mawatateboushi, and up-to-dated sensibility and design.
Ojiya Pongee, woven with hand-spun yarn, displays magnificent harmony with the typical gloss and pleasant feel of silk as well as the simple taste.
[A nationally-designated traditional craft (Designated by the Minister of Economy, Trade and Industry)]
Sponsored by Ojiya Orimono Dogyo Kyodo Kumiai (textile industry cooperative association)
Translation by: Hiroko Okamura, reviewed by Tomoko Yamamoto
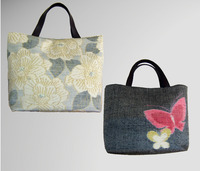
Materials | Doupion raw silk or hand-spun floss yarn |
---|---|
Crafting Processes | How to make yarn:
Materials of yarn: Doupion raw silk, floss and hand spun yarn are main materials of Ojiya Pongee. They represent typical Japanese yarns with refined gloss and feel and have been traditionally utilized as top-class Kimono cloth. Pulling the floss by hand: To pull the floss thinly to make its uniform thickness, and roll around the machine. (hand-span yarn) Twisting yarn: Pull a few doupion raw silk threads, put them together, and then ply them to make strong and uniform thick yarn. Refining: Remove dirt, oil, and sercin of the doupion raw silk. How to make Kasuri textile: The technique of Kasuri making originates in Ojiya Crepe (Chijimi). A square is made based on the selected picturesque design. For dyeing, brush the sumi (India ink) onto the weft placed along the square edge. This “rubbing-in” method enables pattern designing. Square: The use of square started as a technique for dyeing of Ojiya Crepe in the 1680s. The square is made after the lay-out of the width of textile and number of patterns to be used, based on the original Kasuri design. The weft square is made as follows: piling up several 10 to 100 shingles or cardboard sheets as many as needed, shaving flat the surface of the piles, and coping the design on them. When the square is used, each shingle or cardboard sheet is respectively placed along the threads as a square to be used for reference of dyeing. Making Kasuri: Place the squares along the tight-stretched corresponding weft re respectively, mark with sumi the threads where colors change while matching the selvage marks at both ends of the textile. After that, rub the dyestuff into threads. This method has developed the production of the minute Kasuri pattern. Weaving: Weave elaborately matching each thread of the prepared warp with the patterned weft. Handloom-weaving: Ojiya Pongee is mainly characterized by weaving patterns made by full use of weft Kasuri. The weaving requires a lot of patience: putting each weft carefully through the warp set on the weaving machine, weaving a pattern with matching the selvages marked in Kasuri making. Although the power loom has been recently introduced instead of the hand-loom called “Takabata”, the original weaving method has not changed since the Edo period (17-19c). Finishing: Fill the wood vessel,”Kifune” with tepid water. Remove extra glue from the textile in the water and straighten its width, which creates the original texture of silk floss. |
History | Ojiya Pongee has started to be woven, making the most of Ojiya Crepe’s technique since the middle of the Edo period (17-19c). It was originally silk textile of doupion silk which was span out of cocoons for private use. Then the use of the hand-spun yarn or various kinds of threads from silk cocoons enhanced the texture of the Pongee. Furthermore, the design trend toward luxury brought out delicate curves woven with Kasuri pattern of the weft. Not only striped, Kasuri, or plain as well as white Pongee has been woven since the old times. |
Related URL | http://www.ojiya.or.jp/cloth/tumugi/ |
◆Exhibition / Showcase
Ojiya-shi Sougo Sangyo Kaikan Sun Plaza
Jounai 1-8-25, Ojiya-shi, Niigata 947-0028
Telephone: +81(0)258-83-4800
Opening Hours: 9:00a.m. - 6:00 p.m. (Until 5:00 p.m. in winter)
Closed: December 29-January 3