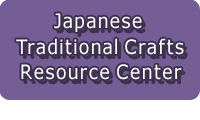
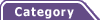
Total:131items
- Pottery & Porcelain (18)
- Lacquerware (4)
- Glasswork (2)
- Wood & Bamboo Work (19)
- Leather Work (1)
- Papermaking (13)
- Textile (20)
- Touzan-Ori: Touzan Weaving
- Sakai Gogatsu Koinobori: Sakai May Carp Streamer
- Nanbu Sakiori
- Nihon Shishu: Japanese Embroidery
- Tsuzurenishiki-Ori: Tsuzurenishiki Weaving
- Ojiya-Tsumugi: Ojiya Pongee
- Ise-Momen: Ise Cotton
- Ojiya-chijimi: Ojiya Crepe
- Yanai-jima: Yanai Stripes
- Kogin-zashi: Kogin embroidery
- Tamba Momen: Tamba Cotton
- Awa Shijira-ori: Awa Shijira Weaving
- Saga Nishiki: Saga Brocade
- Shinshu-Tsumugi: Shinshu-Pongee
- Kyo-nui: Kyoto Embroidery
- Noto Jofu: Noto-jofu hemp fabric
- Matsusaka Momen: Matsusaka Cotton
- Murayama Oshima Tsumugi
- Nibutani-attus
- Oku-Aizu Showa Karamushi Ori: Oku-Aizu Showa Ramie Textiles
- Dyeing products (5)
- Masonry (1)
- Metal Work (11)
- Stationery (4)
- Livingware (3)
- Accessory (4)
- Toys & Entertainment (14)
- Interior (2)
- Other crafts (10)

![]() |
Main Production Site:Nagano |
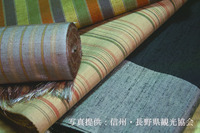
Shinshu pongee is a general term for silk fabrics produced in Nagano prefecture (Central Japan). It has several names such as "Matsumoto pongee", "Yamamayu pongee", "Iida pongee", and "Ina pongee", depending on where the pongee is woven.
The big feature of Shinshu pongee is the folksy dyeing colour of high caliber on the patterns such as stripe, plaid, splashed or plain along with austerely elegant gloss on a textile. This is produced by the traditional dyeing technique using natural dyes.
Another feature is the originality and heart of weavers delicately expressed in each bolt of textile which is woven by the traditional loom called "tebata" using hands and feet, literally handloom in English. Thus every single roll is unique from others.
Main products of Shinshu pongee are "kijakuji", textile rolls for kimonos, and "Obiji", textile for Obi belts, which are woven in various colours and patterns. "Tensan-tsumugi", wild silk pongee only using wild silk yarn, is a specialty of Shinshu region.
In addition to its elegance and warmth, Shinshu pongee is highly reputed for its lightness and durability. Especially its outstanding durability allows people to wear the same Shunshu pongee kimono even for three generations. Wild silk is valued highly as "the queen of fibers" with its shiny emerald colour.
[A nationally-designated traditional craft (Designated by the Minister of Economy, Trade and Industry)]
Information provided by NAGANOKEN ORIMONO KOGYO KUMIAI (Nagano Prefectural Association of Textile Industry)
Translation by Kohei Nishimura, reviewed by Tomoko Yamamoto.
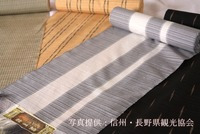
Materials | Raw Silk, Dyes, and so on |
---|---|
Crafting Processes | [1] Boiling cocoons
Put cocoons in cotton bags. In order to remove foreign substances, boil the bags in a cauldron with a supernatant liquid of straw ash solution (a lye) or a liquid containing soda ash, sodium sulfite, or sodium carbonate. [2] Spreading and layering the cocoons After boiling cocoons, wash them with water. Spread a cocoon with fingers and then place it on the back of the hand. After repeating the process three or four times, place the spread cocoons on the wooden frame. One sheet of floss silk consists of nine to twelve cocoons. [3] Spinning yarns There are two ways to spin yarns from sheets of floss silk: (1) roll the sheets on the wooden stick and then pull and spin the floss by hand; (2) put the sheets on the electric spinning machine and then pull out the floss and set on the machine to reel the yarn. Usually, warp yarns are spun slightly thicker than weft yarns. [4] Twisting yarns Prepare paralleled raw or doupion silk yarns in required thickness. Then reel yarns on the stick and put them into water to soften sericin included in them. Twist yarns with the traditional silk throwing machine called hatchonenshiki, and re-reel them into skeins. [5] Refining skeins Put the twisted skeins into cotton bags, or hook them on sticks. Then scour them in the refining cauldron for 40 - 50 minutes with refining agent such as a lye or a liquid containing sodium carbonate. [6] Dyeing Dye the reeled yarn. There are two ways of dyeing: traditional vegetable dyeing and modern chemical dyeing. [7] Designing Develop a design for a textile. [8] Preparing ground yarn ('taneito') In Shinshu region, people copy designs to base yarns on the traditional pattern-designing board called "Osadai-jogi". Place a design sheet on the board and bridge the white cotton yarn on the comb-like reed splits called "osaha". Then copy the underlying design to the base yarn with India-ink. [9] India-inking Allocate the base yarn onto the extended warp and weft yarns. Mark the yarns with India-ink using a spatula according to the marks of the base yarn. [10] Tying the inked parts with hands Tie the India-inked parts tightly with cotton threads so that tied parts will not be dyed when the whole yarn is dyed. [11] Arranging the warp yarn Cut the warp yarn into the required number of yarns and reel them on the beam. [12] Weaving Pass the warp yarn through the heald and the reed. Open the handloom vertically, insert the shuttle of the weft yarn, and beat up the inserted yarn with the reed. When weaving with the inked yarn, we usually use both the inked yarn and the normal (not-inked) yarn at the same time. Finally, Shinshu pongee is finished after being woven with a careful artisanship and tightened to produce its thickness and elasticity. |
History | From the early Edo period (17-19c), domains in Shinshu region (present Nagano prefecture) had been encouraged to develop sericulture as an industrial policy of the Tokugawa shogunate. Since then, textiles woven with raw silk yarn and floss silk yarn have been produced as farmers' secondary job. This is said to be the origin of the Shinshu pongee.
At the same time, the techniques of vegetable dyeing started spreading because Shinano region was rich in naturally growing vegetable-dyeing materials. In 1748, people started shipping their pongee textiles to Kyoto. Records show that they have shipped the textiles almost every year from 1751 to 1772. It was not until the end of the Taisho period (20c) that the pongee was commercially produced. Later, although the popularity of the pongee textiles once declined, the production of Shinshu pongee has revived in the region in the post-war era, thanks to the promotion measures of local authorities concurrent with the pongee boom. Subsequently, the status and popularity of Shinshu pongee has been increasingly rising as a luxurious textile until today. |
◆Exhibition / Showcase
Naganoken Orimono Kogyo Kumiai
(Nagano Prefectural Association of Textile Industry)
C/O Kubota Shokusen Kogyo .Co
2-29, Higashimachi, Komagane City, Nagano Prefecture, 399-4106
Tel +81-265-83-2202 / Fax +81-265-83-2204 (Japanese only)
Assistance needed? For inquiries in English:
JTCO Contact Form
Your inquiries will be forwarded by JTCO in Japanese to the organization you wish to contact.
Please specify the name of the craft/art you wish to inquire about.