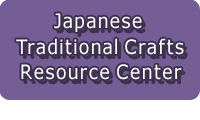
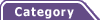
Total:131items
- Pottery & Porcelain (18)
- Lacquerware (4)
- Glasswork (2)
- Wood & Bamboo Work (19)
- Leather Work (1)
- Papermaking (13)
- Textile (20)
- Dyeing products (5)
- Masonry (1)
- Metal Work (11)
- Stationery (4)
- Livingware (3)
- Accessory (4)
- Toys & Entertainment (14)
- Interior (2)
- Other crafts (10)

![]() |
Main Production Site:Aomori |
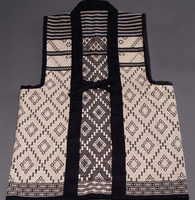
Kogin-zashi is embroidery technique applied on indigo hemp cloth with white cotton yarn, which reinforces the durability of the texture as well as retaining heat.
Compared to Sashiko, famous quilting technique in Japan, Kogin-zashi is rather embroidery work that cotton yarn is stitched into the meshes on the fabric, which makes geometrical pattern. Each running stitch is horizontally sewed and the length is determined by the number of the warp.
After the hemp cloth is weaved and dyed with indigo, embroidery is done stitch by stitch with thick cotton yarn on the fabric.
It is easy to explain by words. However, its hard work which needs a lot of time is beyond our imaginings. Even needlework on a postcard size cloth needs one week at least.
Kogin-zashi is classified into three types according to the areas they are made.
Nishi (west) Kogin
Products made in the west part of Hirosaki city - Nishimeya village former Souma village,(integrated into Hirosaki city in 2006), , Funazawa district and Kozawa district in Hirosaki city are called "Nishi Kogin".
"Nishi Kogin" has stripe patterns on its shoulder, which reinforces the cloth in order to withstand hard use in the mountain.
Since "Nishi Kogin" has stripes of five layers which is stitched with black and white threads, it is also called "Shima Kogin"
The hemp cloth itself is originally fine, which is tough for sewing and the delicate work to make various fine patterns needs patient effort. This is why "Nishi Kogin" was used for festive kimono.
Because of the beauty of the festive kimono, there was a saying in Tsugaru district that "It should be from the west area, if you take a wife".
Higasi (East) Kogin
Products made in Kuroishi city, Former Kyuonoe and Kyuhiraga town (integrated into Hirakawa city in 2006)and Ishikawa distinct in Hirosaki city are called "Higashi Kogin"..
Many Higashi Kogin embroideries are made on hemp cloth weaved with thick hemp thread. And the large-patterned product without stripe is its feature.
Sanko (Three stripes) Kogin
Products of Sanko Kogin are made in Former Kanegi town (now Goshogawara city), Kizukuri town (now Tsugaru city) and Shariki village (now Tsugaru city). .
The products are characterized by three conspicuous thick stripes and are also popular for its excellent designs.
Since there are only a few existing products at present, products of "Sanko Kogin" have rarity value. It is not certain about the reason but it is said cold-weather and poor harvest often caused serious damage to Kanagi district, which made it difficult for the residents to make Koginsashi.
[Traditional handcraft of Aomori prefecture]
Information provided by Hirosaki KoginKenkyujo (research institute)
Translation: Mana Hara, reviewed by Naoko Yamashita
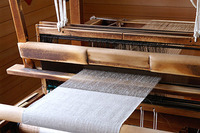
Materials | Hemp cloth, cotton thread |
---|---|
Crafting Processes | Process
【1】Twisting thread 【2】Dyeing (indigo dyeing, plant dyeing, chemical dyeing) Boiling ( removing oil out of thread) → drying → dyeing → starching → drying 【3】Weaving Deciding the length of warp on a warper,which has poles called “Aya” on it, so that warp does not get entangled each other. → Omaki(The warp is stretched and looped around lease rods) → Soukou (Warp threads are threaded through the heddles) and the threads are inserted into a reed called “Osa” which is made of gold and bamboo to prepare for weaving, → weaving on Takahata ( loom) 【4】Fixing 【5】Cutting 【6】 Embroidery work Sew stitches onto the cloth according to the pattern 【7】Finishing Kogin-zashi product is finished after ironing and finishing treatment. |
History | It is said that Koginsashi started in Edo period (17-19c), when wearing cotton clothes was not allowed to farmers according to the hierarchy of samurai, farmers, artisans and merchants.Hemp cloth was allowed to wear instead, however, it was not warm enough to prevent cold. People in Tsugaru thought about what they could they do to keep warm even with thin fabric and get through harsh cold winter in Tsugaru. The cloth must be durable during farm work.
To clear such conditions, farmers came up with an idea of "Kogin" embroidery, using cotton thread which was prohibited its use for clothes. This was the wisdom of farmers. Long winter in Tsugaru gave them time for delicate and beautiful needle work. This handiwork also became pleasure for daughters, where they could express themselves. In the middle of Edo era, cotton thread became more available and people competed to make luxurious Kogin-zashi. Eventually, people started to use Kogin-zashi as their festive kimonos as well as their daily wears, and even brides prepared Kogin-zashi kimono when they got married. |
◆Exhibition / Showcase
Hirosaki Kogin Kenkyujo
Zaifu-town 61, Hirosaki-city, Aomori-Pref
036-8216
TEL: +81-(0)172-32-0595 FAX: +81-(0)172-32-0850
(Japanese only)
Assistance needed? For inquiries in English:
JTCO Contact Form
Your inquiries will be forwarded by JTCO in Japanese to the organization you wish to contact.