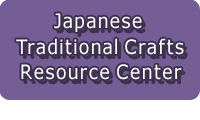
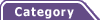
Total:131items
- Pottery & Porcelain (18)
- Lacquerware (4)
- Glasswork (2)
- Wood & Bamboo Work (19)
- Leather Work (1)
- Papermaking (13)
- Textile (20)
- Dyeing products (5)
- Masonry (1)
- Metal Work (11)
- Satsuma Suzuki: Satsuma Tinware
- Tosa Uchihamono: Tosa Blade
- Kaga Zougan: Kaga Inlay
- Akita Ginsen Zaiku: Akita Filigree
- Token: Japanese Sword
- Banshu-gama : Banshu Sickle
- Echigo-Sanjo Uchi Hamono: Echigo-Sanjo Blade
- Osaka Naniwa Suzuki: Pewter/Tin Ware
- Nakaniida-Uchihamono: Nakaniida Traditional Blade
- Higo-Tsuba
- Nokaji Hamono: Nokaji Blades
- Stationery (4)
- Livingware (3)
- Accessory (4)
- Toys & Entertainment (14)
- Interior (2)
- Other crafts (10)

![]() |
Main Production Site:Kagoshima |
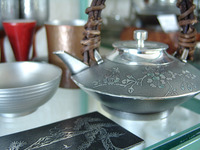
The traditional attraction of Satsuma Tinware lies in the aesthetic quality of its casting surface called nashiji-hada (pear-skin like surface), and the quality of the product is determined by its first production process called ikomi (casting).
The crystal structure of the metal, produced when molten tin is poured into a mold, becomes the surface of tinware and cannot be modified in the later processes. During this process, a traditional craftsman holds his breath when slowly pouring tin into a mold.
When watching him throwing himself into work, you will find marks like insect bites on his arms and chest. These are burn scars caused by splashes of molten tin.
Tinware is a craft made with arts (molding and surface finish), casting theory of production technology, lathe cutting (machining), etching (chemistry), printing technology, and lacquering (paint).
[A traditional craft designated by Kagoshima Prefecture]
Source: Ohtsuji-asahidou
Translation by: Tomoe Ukida, reviewed by Tomoko Yamamoto
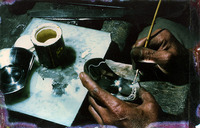
Materials | Tin |
---|---|
Crafting Processes | 1. Fusion
Melt a tin ingot in an iron pot on a gas stove. 2. Mold making Put an outside mold and a core (mold) together, pour molten tin from a casting port or sprue, and take it out when it becomes solid. To make a traditional mold of Satsuma, first make a pattern of a product. Set a piece of unseasoned wood, which is easy to shave, on a horizontal lathe, scrape it, then adjust heavy paper into a shape of the central part. This papier-mache mold will be used as an important pattern (gauge) for the outside mold of the product. 3. Rough cutting Attach the molded tin to a wooden mandrel of the lathe and shave the inside and outside of eccentric and rough casting surfaces. In Kagoshima, horizontal lathes are used. A craftsman stands in parallel to the lathe and shave the surface with a jack plane under his arm while using the plane stock as a fulcrum. One jack plane, five or six smoothing planes, and five or six smaller smoothing planes are effectively used to shave tinware. A craftsman who uses the planes forges and sharpens them. The surface becomes beautiful because the plane is placed obliquely to the cutting surface to shave just like cutting sashimi (sliced raw fish) by pulling a knife. As the planes are constantly sharpened, the edge faces retain a mirror surface. Compared with a vertical lathe, a horizontal lathe has a wider operation range and can shave various objects from a small one to a big one including a long one. 4. Intermediate cutting Shape the tinware with a smoothing plane. 5. Engraving Engrave the maker's name on the back bottom part. It is engraved when the outside is shaved. The reason is that this process requires a metal plug and scratches cannot be flattened or scraped off after the tinware is completed. 6. Joining (Soldering) Solder each part made through the above processes. Tinware is created by soldering. 7. Shaving Shave the tinware into a mirror-finished surface. As shaving cannot be done after etching, craftsmen have to concentrate on their work and this is a very important process in which determine the quality of the tinware. 8. Painting Draw a design with resist ink, a paint which is resistant to dilute nitric acid. Cubic curves or places where a brush cannot reach can be phototypeset if a client orders with a manuscript including patterns, characters, logos, and crests by fax or email. 9. Matting (Etching) Soak the tinware in adjusted dilute nitric acid for a predetermined time to make nashiji-hada (pear-skin like surface). After adjusting the concentration of dilute nitric acid and the temperature, a craftsman soaks the tinware in the solution. He confirms that the surface becomes like a pear-skin as expected, and then soak it in the sodium hydrogen carbonate solution (baking soda). (Neutralization) 10. Finishing Set the tinware on a lathe to finish the surface. A frosted product is completed with this process. 11. Ibushi (coloring) Mix black lacquer with pigments, lacquer the surface uniformly, and dry it in a room (Polymerization). 12. Ibushi finishing (Black finish) Set it on a lathe to polish the surface. An ibushi product is completed. |
History | [History of tinware]
The Chinese character "錫" meaning tin was created in China. When the left-hand radical "金" is removed, "易" is left. "易" is said to mean white. We have colors called gold, silver, and copper, but not a color called tin. It is rare that a metal oxidizes at high temperatures, but hardly at normal temperatures with its colorless compound. When hard and dense platinum and stainless steel are polished, for example, they shine like a mirror but still give a hard and cold impression. Compared with them, the reflection of tin is not silvery-white but soft white, making us feel gentle and warm. [History of Satsuma Suzu-ki (Tinware)] The origin of tinware making in Satsuma goes back to the time when a vein of tin was discovered by Yagi Mondonosuke Motonobu in a tin mine, deep in Taniyana, 20 kilometers south of Kagoshima City in 1655 and the lord of the Satsuma domain Shimazu Mitsuhisa obtained the permission of mining in 1701. This brought Satsuma nationwide recognition for its tin and tinware. It is believed that the tinware began to be made in Satsuma after 1813 when the Taniyana-kozan mine began producing more tin. In Saiyuki (Journey to the West) by Tachibana Nankei, which is said to be the representative work of travel literature in the Edo period (17-19c), he wrote, "In the castle town of far-away Satsuma Province, there were no ceramic bottles, but all bottles were made of tin." Another type of tinware production brought from China to Kyoto developed in Osaka as a producing area. This is the origin of Naniwa Suzuki tinware with its branch schools in other areas and its production method is different from that of Satsuma Suzuki. |
◆Exhibition / Showcase
Assistance needed? For inquiries in English:
JTCO Contact Form
Your inquiries will be forwarded by JTCO in Japanese to the organization you wish to contact.