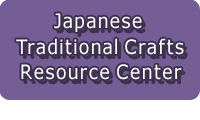
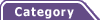
Total:131items
- Pottery & Porcelain (18)
- Lacquerware (4)
- Glasswork (2)
- Wood & Bamboo Work (19)
- Leather Work (1)
- Papermaking (13)
- Textile (20)
- Touzan-Ori: Touzan Weaving
- Sakai Gogatsu Koinobori: Sakai May Carp Streamer
- Nanbu Sakiori
- Nihon Shishu: Japanese Embroidery
- Tsuzurenishiki-Ori: Tsuzurenishiki Weaving
- Ojiya-Tsumugi: Ojiya Pongee
- Ise-Momen: Ise Cotton
- Ojiya-chijimi: Ojiya Crepe
- Yanai-jima: Yanai Stripes
- Kogin-zashi: Kogin embroidery
- Tamba Momen: Tamba Cotton
- Awa Shijira-ori: Awa Shijira Weaving
- Saga Nishiki: Saga Brocade
- Shinshu-Tsumugi: Shinshu-Pongee
- Kyo-nui: Kyoto Embroidery
- Noto Jofu: Noto-jofu hemp fabric
- Matsusaka Momen: Matsusaka Cotton
- Murayama Oshima Tsumugi
- Nibutani-attus
- Oku-Aizu Showa Karamushi Ori: Oku-Aizu Showa Ramie Textiles
- Dyeing products (5)
- Masonry (1)
- Metal Work (11)
- Stationery (4)
- Livingware (3)
- Accessory (4)
- Toys & Entertainment (14)
- Interior (2)
- Other crafts (10)

![]() |
Main Production Site:Chiba |
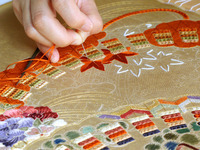
Japanese embroidery has been passed down over 1600 years.
People have embroidered on Japanese traditional dresses, robes, Noh and Kabuki costumes as well as other various kinds of commodities. The Kanji character for “picture” is composed of two parts, one meaning “thread” and the other meaning “to meet.” If directly interpreted, this character means “to meet threads.” As this interpretation suggests, it is likely that people used thread to make a pattern in olden times when paintbrushes were not available. We can see that thread has been familiar to Japanese people’s lives for a long time.
[A Traditional Craft Designated by Chiba Prefecture]
Source: Kurenai-kai
Translation: Marina Izumi, reviewed by Catherine Newman
Materials | Silk cloth / silk thread / gold thread |
---|---|
Crafting Processes | [Process of making Japanese embroidery]
(Make stencil paper and draw a rough sketch) A draft of the embroidery is made onto a stencil paper, and then the design is drawn on silk cloth. (Coloring) By placing colored threads on silk cloth, the colors are selected considering the draft and design. Factors such as the pattern, season and age-group are also taken into consideration. Colors for some parts are determined during the process of embroidering. (Embroider) It is only after colors are arranged that embroidery can be started. Japanese embroidery has 43 ways of embroidering. They are selected depending on the pattern and usage. They vary in terms of thickness, bulge and have sections including how to embroider dots, lines, faces and how to embroider stereographically. Only those who are knowledgeable about each characteristic can select the style of embroidery suitable for a particular part. This requires great skill. (Give a finishing touch) After it is embroidered, the work has its finishing touches while kept placed on an embroidery frame. Embroiderers make sure all parts have been embroidered, cut the threads on the reverse, paste on wheat starch, and then smooth the silk cloth with steam. This process prevents threads from fraying and enables them to be glossy. [Technique] Japanese embroidery has 43 ways of embroidering. Skills of expression can be developed endlessly by mastering the meanings and functions implied in their name. The tradition of embroidery inherited with its long history could be described as “embroidery techniques as well as the thoughtful mind required for its expression.” Taking a long time, each stitch is delicately made on a silk cloth which is considered a precious jewel among fabrics. [Tools for Japanese Embroidery] 1. Needles and a pincushion Needles specially used for Japanese embroidery and a felt pincushion for easy use 2. Teko-Hari A needle used for resolving distortion of threads and making them glossy 3. Scissors Sharp scissors for Japanese embroidery that cut well 4. A perforator A perforator used to twist threads and to prepare an embroidery frame 5. Koma A tool used for “Komatori-Nui,” one technique of embroidering |
History | Japanese embroidery, which has more than 1600 years of long history, has been passed down on in the daily lives of people. Excellent Japanese embroidery must be great in 4 aspects including embroidery techniques, designs, color arrangements and the selection of the embroidering method. These 4 aspects have been cultivated and inherited to date throughout Japan’s long history. To explain its history simply, Japanese embroidery started for practical reasons such as repairing and reinforcement in the primitive age. It developed as techniques for embroidering Buddhist images (the Asuka and Kamakura period), absorbed designs from overseas (the Nara period), Japanized those designs and deepened its coloring beauty in the process of arranging colors for women’s robes (the Heian period), and reached its extremity (the Muromachi period).
It is in the Momoyama period that Japanese embroidery started to decorate Kosode, a basic Japanese robe, mixing all the accumulated techniques, designs and colors. Thick and durable stitches suitable for obi (a thick sash) developed in the late Edo period. It was in the Meiji and Taisho period that Japanese embroidery developed by absorbing unique stitches often seen in foreign embroidery. As this history shows, Japanese embroidery has changed greatly over time depending on what the commodity to be embroidered on is, and has also developed in close connection with people’s lives of the past. |
Related URL | http://kurenai-kai.jp/index.html |
◆Event Information
Kurenai-kai Exhibition Information (Japanese Only)
Period of exhibition: every spring
Place: Tokyo, Nagoya and Osaka